Following the piloting process of Advanced Manufacturing Labs for H/VET through the Collaborative Learning Factory (hereafter CLF), the EXAM4.0 partners we have piloted 16 technologies embedded in Industry 4.0.
The following image shows the overall structure of the piloting process.
Labs for Advanced Manufacturing-CLF
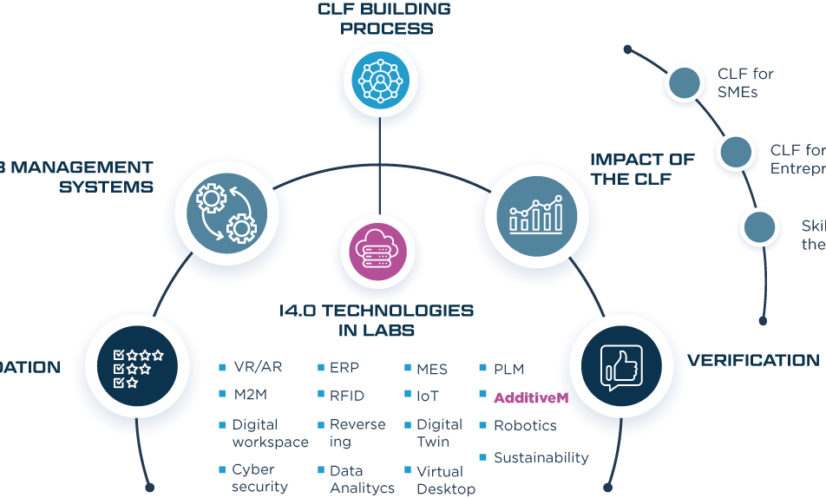
The present report is the one out of 16 I4.0 technology described within the “Industry 4.0 technologies in labs” section, specifically #10 Additive Manufacturing
DEFINITION AND APPLICATION OF ADDITIVE MANUFACTURING IN INDUSTRY
Additive Manufacturing, also called 3D-printing, is a production method that uses a layer by layer technique to manufacture products. Additive Manufacturing works in the most common cases, by either having a powder bed which is sintered with a laser beam or by adding material to a building plate one layer at the time. In both cases one ultra thin layer is added upon the other, ultimately resulting in a fixed 3D-object. Hence does Additive Manufacturing add material when producing components, compared to most other manufacturing methods where material is removed in order to create the final product instead. Additive Manufacturing is based on a 3D-model, in most cases CAD-files exported into STL- files. The CAD-files are simply inserted into a “packing” software that communicates with the printer, the printer will then replicate this file by adding layer after
layer of material.
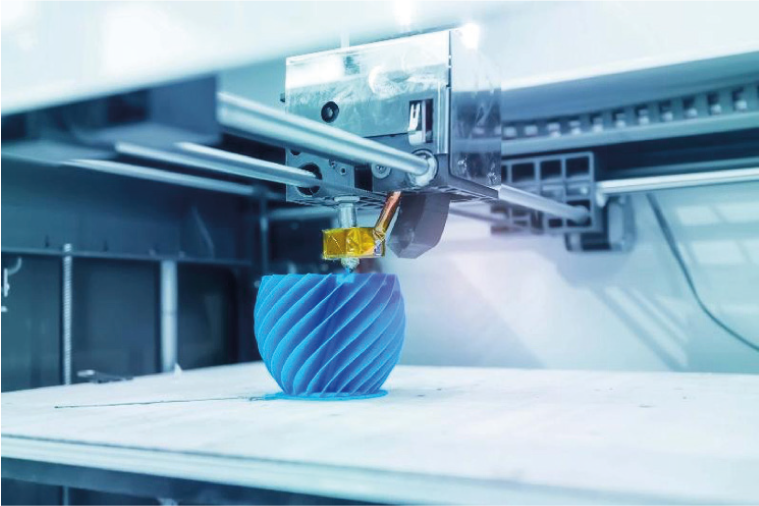
Figure 2: 3D printer printing. Source: SMC
There are a variety of different additive manufacturing processes:
- Powder Bed Fusion: Powder Bed Fusion (PBF) technology is used in a variety of Additive Manufacturing processes. These systems use lasers, electron beams or thermal print heads to melt or partially melt ultra-fine layers of material in a three-dimensional space. As the process concludes, excess powder is blasted away from the object.
- Material Jetting: A print head moves back and forth, much like the head on a 2D inkjet printer. However, it typically moves on x-, y- and z-axes to create 3D objects. Layers harden as they cool or are cured by ultraviolet light.
- Binder Jetting: This is similar to material jetting, except that the print head lays down alternate layers of powdered material and a liquid binder.
- Material Extrusion: It is one of the most well-known additive manufacturing processes. Spooled polymers are extruded, or drawn through a heated nozzle mounted on a movable arm. The nozzle moves horizontally while the bed moves vertically, allowing the melted material to be built layer after layer. Proper adhesion between layers occurs through precise temperature control or the use of chemical bonding agents.
- Directed Energy Deposition: It is similar to material extrusion, although it can be used with a wider variety of materials, including polymers, ceramics and metals. An electron beam gun or laser mounted on a four- or five-axis arm melts either wire or filament feedstock or powder.
- Sheet Lamination: Laminated object manufacturing (LOM) and ultrasonic additive manufacturing (UAM) are two sheet lamination methods. LOM uses alternate layers of paper and adhesive, while UAM employs thin metal sheets conjoined through ultrasonic welding. LOM excels at creating objects ideal for visual or aesthetic modeling. UAM is a relatively low-temperature, low-energy process used with various metals, including titanium, stainless steel and aluminum.
- Vat Polymerization: With vat photopolymerization, an object is created in a vat of a liquid resin photopolymer. A process called photopolymerization cures each microfine resin layer using ultraviolet (UV) light precisely directed by mirrors.
ADDITIVE MANUFACTURING IN HVET/VET LABS
In this section we describe how Additive Manufacturing can be implemented in VET/HVET-centre labs. Different options and applications are described.
There are numerous learning possibilities when it comes to Additive Manufacturing at VET-centres.
A 3D-printing machine works as mentioned previously, by inserting a 3D-file into a software that is connected to the machine, the machine will replicate this file in order to manufacture the products. Additive Manufacturing opens up new manufacturing possibilities which are difficult to obtain with other production methods. 3D-printing makes it possible to create complex designs such as internal fixtures. It does however come with requirements as well, and these requirements vary depending on the type of machine and the 3D-printing method that is used.
For example, support material must be added in the majority of all 3D-printing machines. This applies, in most cases, to machines that place material on a building plate or machines that print with metal, machines with powder bed fusion do, most often, not need support material. One learning possibility is therefore for students to think beyond the traditional thinking when it comes to designing products, and learning how to design new products for 3D-printing or use the benefits that comes with 3D-printing for product development.
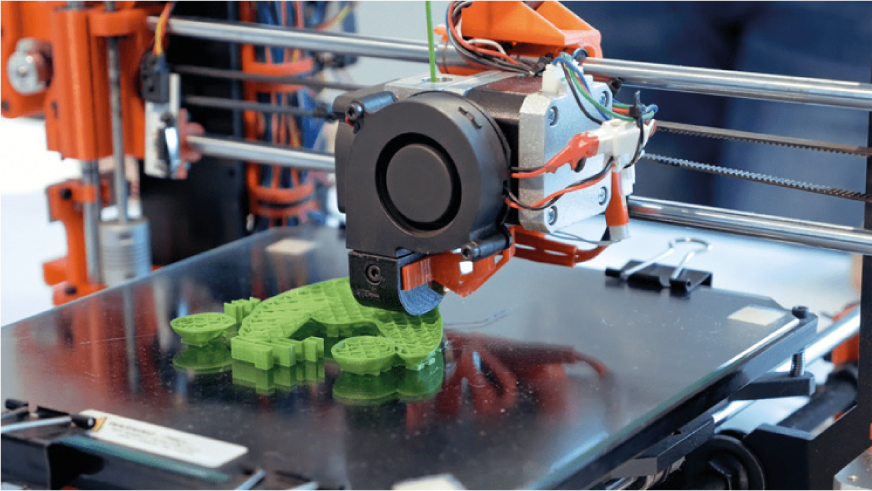
Figure 2: 3D printer working. Source: https://ecolink.com/info/why-is-it-called-additive-manufacturing/
Another important aspect is the hands-on learning of the machines. The students will learn how to handle the machines in the lab, including aspects like manoeuvring the software and cleaning machines as well as maintenance. These factors will make the students independent in the whole process of manufacturing products via Additive Manufacturing.
Curt Nicolin Gymnasiet has implemented different 3D-printers in the labs at the school. The variety of printers ensures the possibility of teaching different methods.
The largest owner company of the school is heavily investing in SLM 3D-printers. Curt Nicolin Gymnasiet has a scale-down learning factory of this company’s 3D-printing workshop. It uses a similar machine, from the same brand, but with nylon as material instead of metal. The process from idea to finished product in Curt Nicolin Gymnasiet’s learning factory is very similar to the one at the company workshop.
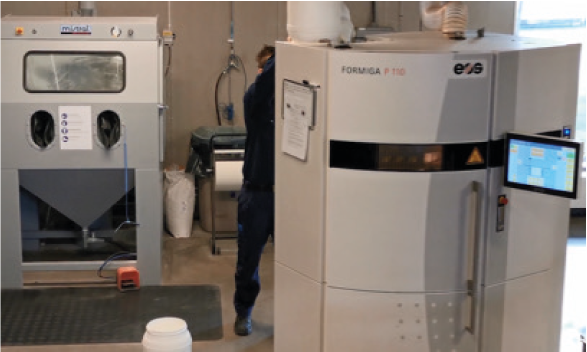
Figure 9: Curt Nicolin Gymnasiet 3D printing machines. Source: Curt Nicolin Gymnasiet
Curt Nicolin Gymnasiet has implemented numerous FFF 3D-printers in the labs. These are more economical to use and are therefore even more beneficial for education. They are useful for students to produce both prototypes and products for school projects. They also show that there are different methods regarding Additive Manufacturing available and the students will learn which method is beneficial for different purposes.
This printer has been adapted to I4.0 by connecting it to the Internet and adding a camera, making it possible to start and operate it from anywhere. The printer is also connected to a PLC, and a collaborative robot can start the printer as well as change the building plate.
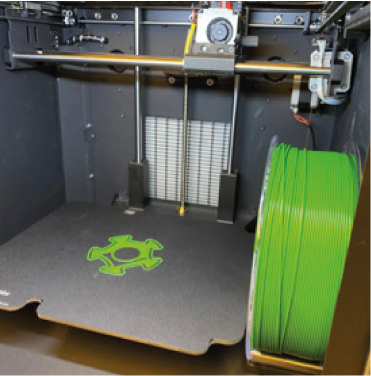
Figure 4: 3D printer adapted to I4.0 in Curt Nicolin Gymnasiet. Source: Curt Nicolin Gymnasiet
Tknika’s Additive Manufacturing (AM) lab is part of the net of AM lab programme IKASLAB of the Vocational Education and Training Basque System. It includes 20 VET Centers in the Basque Country.
Tknika’s IKASLAB works only with teachers and it has been introducing industrial equipment in order to test, practice and learn from different AM technologies and applications:
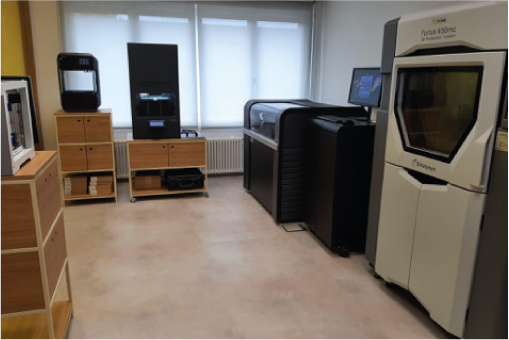
Figure 5:Tknika’s Ikaslab machines (FDM, Polyjet and ADAM). Source: Tknika
Stratasys FDM technology (filament), Stratasys Polyjet J750 DAP (resin), HP Multijet Fusion 4210(powder), Formlabs 3BL (resin), Markforged Metal X (metal filament).
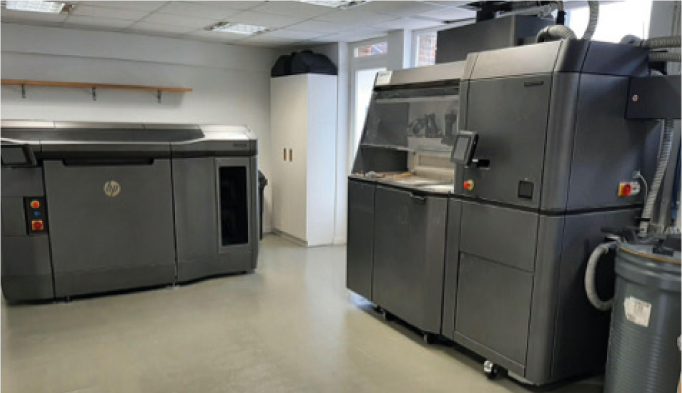
Figure 5: Tknika’s lab for HP Multijet Fusion technology. Source: Tknika
The aim of Tknika´s lab is to introduce Additive Manufacturing in education through 2 lines of work:
- The management of the net of labs, by sharing experiences where AM is introduced to teachers and students in all sorts of studies.
- Obtain knowledge of advanced applications by the development of projects including the practice with industrial additive manufacturing equipment of Tknika, by teachers of all the net of AM labs: learning by doing.
The CLF that is going to be launched has divided its production process into 4 stages (product design, process engineering, production and assembly) as can be seen in the following image. Within these stages, additive manufacturing is going to be incorporated in the production stage
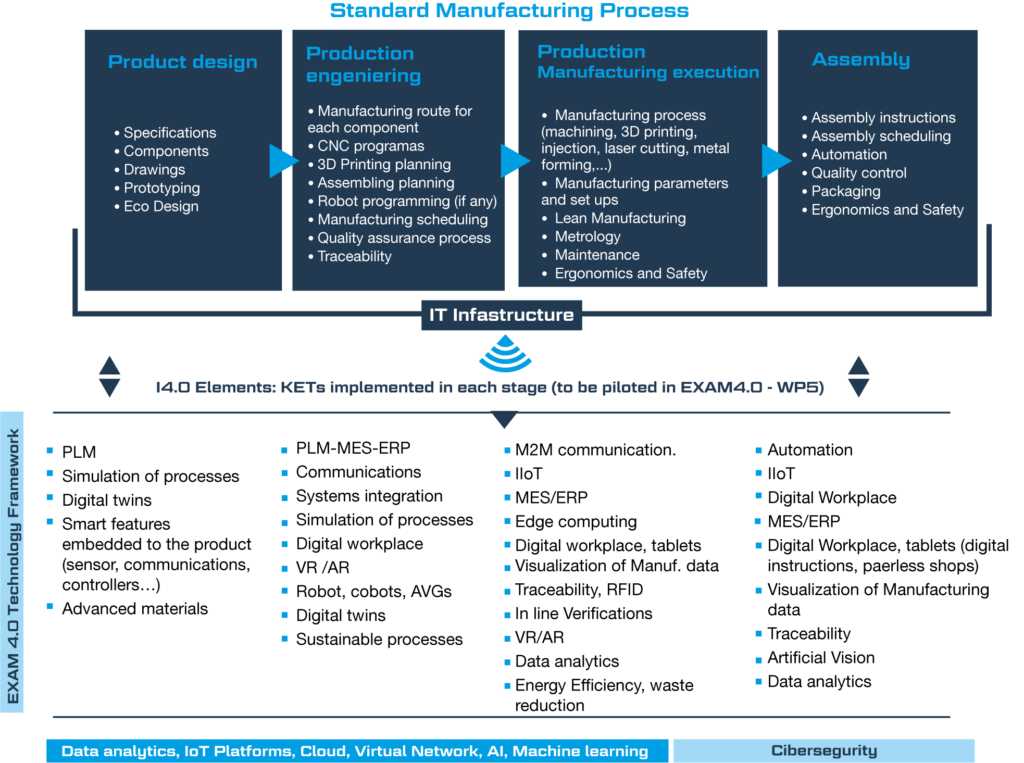
Figure 7: EXAM4.0 CLF value chain Source: Author’s creation
Additive Manufacturing plays a key role in the EXAM 4.0 CLF as the main production method for the products of the EXAM robot. Additive manufacturing is used both for the production of prototypes and the actual components produced in the collaborative learning factory. Additive Manufacturing is a very effective method for producing plastic components in low quantities and is therefore the superior option for the EXAM robot.
Additive Manufacturing will have another important role within the CLF, except for producing parts for the EXAM robot. Additive Manufacturing is a growing business but yet quite expensive to invest in for educational purposes. Additive Manufacturing, together with other important technologies that are included in the CLF, will be available for partners who do not have advanced manufacturing resources themselves.
When it comes to inserting additive manufacturing into the CLF it allows the creation of lighter, more complex designs that are too difficult or too expensive to build using other machining techniques. In the CLF, by not having a production of large runs, gives you the ability to create complex unit parts cheaply and with adequate mechanical properties. It is also a suitable tool when it comes to creating customizations in the robot.
It also excels at rapid prototyping. Since the process eliminates intermediate steps, modifications are possible on the fly. It offers a more dynamic process, being able to test and discover improvements.
According to student’s competences, they will practice their creativity skills by designing parts for Additive Manufacturing, thus thinking beyond the traditional way of designing products for production. Students will learn DfAM (Design for Additive Manufacturing).
The method DfAM removes the limitations of conventional manufacturing. Students will upskill their technical expertise by operating the additive manufacturing machines and equipment.
Critical thinking can be explained as the analysing of facts to form a judgement (Wikipedia, 2021). Additive Manufacturing is a relatively new production method, which leads to new problems and challenges. It is therefore important to have good critical thinking in order to make good decisions out of new information. New problems also result in the requirement to improve problem solving skills in order to come up with quality solutions to these issues.
It is possible to produce parts in various materials when it comes to Additive Manufacturing. This requires material handling skills. Some metal powder that is used are only the size of 0.015 to 0.045 mm, and these particles result in health risks. This requires extreme material handling skills as well as safety skills.
COLLABORATION OPPORTUNITIES OPENED BY ADDITIVE MANUFACTURING
Given the need for speed, adaptation, flexibility and low costs in manufacturing processes, ‘additive manufacturing’ emerges. These attributes make it a suitable tool for collaboration between different centers.
First of all, it is a suitable tool for solving different problems or errors that may appear in the robot. The possibility of manufacturing complex parts quickly and easily means that any failure or improvement of the product is solved in an efficient way. As you work on CAD files,
these solutions can be sent to other centers instantly.
On the other hand, robot improvements can be worked on between teams from different centers.
In addition, these attributes also make it a tool that enables product customization, since each center can create different accessories for the different uses they have. In turn, groups could be created to develop solutions to emerging needs.