Following the piloting process of Advanced Manufacturing Labs for H/VET through the Collaborative Learning Factory (hereafter CLF), the EXAM4.0 partners we have piloted 16 technologies embedded in Industry 4.0.
The following image shows the overall structure of the piloting process.
Labs for Advanced Manufacturing-CLF

The present report is the one out of 16 I4.0 technology described within the “Industry 4.0 technologies in labs” section, specifically #9 Robotics.
DEFINITION AND APPLICATION OF ROBOTICS IN INDUSTRY
Industrial robotics and automation are the pillars that have made the consolidation of Industry 4.0 possible, in addition to bringing along numerous benefits for the productivity and efficiency of production resources.
The different models of industrial automation that are established today, eliminate the subjective factor of human decisions, achieving lower margins of error and more precise processes, at the same time that they free human workforce from repetitive or dangerous tasks.
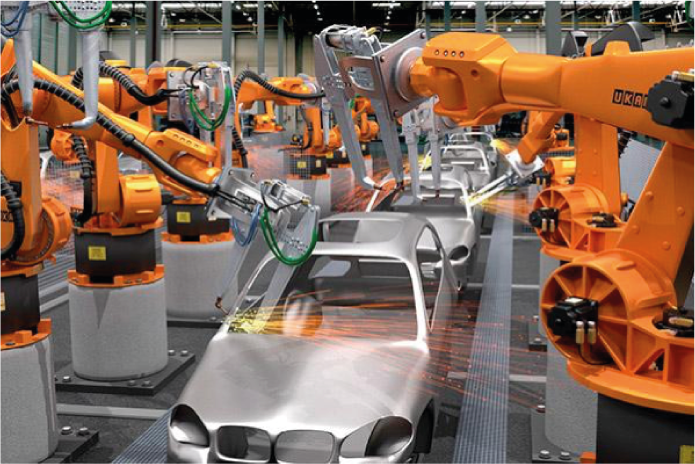
Figure 1: Robots working on a car manufacturing line. Source: https://www.atriainnovation.com/en/robotica-industrial-tradicionales-colaborativos-y-adaptativos/
Countless manufacturers use industrial robots to automate tasks, improve worker safety, and increase overall production, while reducing waste and operating costs. With the increasing prevalence of industrial robots in manufacturing environments, there has been an increase in demand for many different types of industrial robots to suit specific applications and industries (Avansis, 2021).
Depending on the type of industry and manufacturing or production needs, the types of industrial robotics or automation are:
- Fixed: the machine or robot is designed and programmed to perform the same task without interruption. In large-scale or mass manufacturing or production, it is the most widely used type for automating simple and highly repetitive tasks that require precision.
- Programmable: the machine or robot is designed in such a way that it is easy to reconfigure or reprogram it so that it can carry out different tasks. It is the most widespread type of automation in manufacturing or production lines for different product models.
- Flexible: industrial robots work in an orchestrated or coordinated manner by a central system that controls them based on the information they provide.
If we take into account the applications and uses of robots in industry, we can see that this is very broad. In the health field, industrial robots or automated systems are used to facilitate the work of professionals in activities or performing surgeries that require great precision and where an error can be fatal.
In the manufacturing industry, such as the automobile industry, to increase productivity and quality by automating repetitive and simple tasks in the production chain.
In other fields such as the military, agriculture, security, food production, among others, industrial robotics is beginning to be used more and more for different tasks or activities (UNIR, 2021).
If we take into account the manufacturing process, industrial robots with various intelligent and sensory capabilities are utilized there. In an Industry 4.0 factory, the robots endowed with the advanced capabilities owing to the information, networking and sensor technologies are able to collaboratively work with human workers and cooperatively with the other robots in an assembly line. The collaborative and cooperative working applications of the robots, the maintenance practices and assembly line applications using the robots shape the factories of the future (Alp Ustundag, 2018).
In the market we find several types of industrial robots, which we can classify according to the type of movement they perform in. Some of them are (Engineering, 2021):
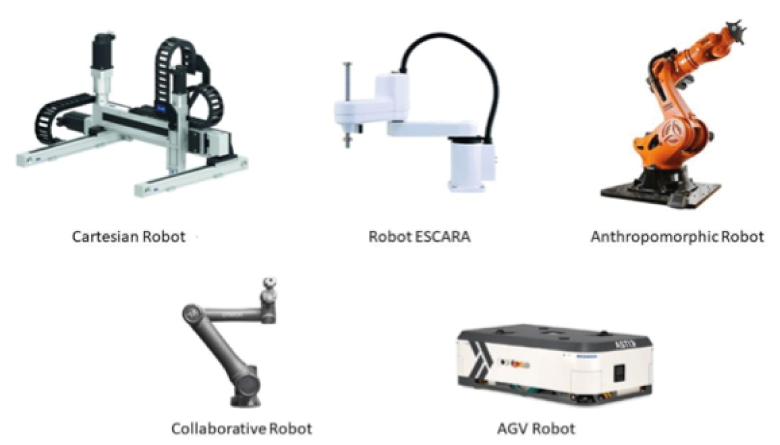
Figure 2: Types of robots. Source: https://www.vld-eng.com/blog/tipos-de-robots-industriales/
- CARTESIAN ROBOT: It is an industrial robot whose 3 main control axes (X, Y, Z) are linear and form right angles to each other. Its structure can be of the cantilever or gantry type. They are very fast, precise, easy to control and have a high load capacity. They are used in applications that require high precision linear movements. Its main applications are handling, storage, palletizing, loading and unloading.
- ROBOT SCARA: It is an industrial robot with 4 freedoms of movement, X, Y, Z being the rotating Z axis. These robots are known for their fast working times, their high repeatability, high load capacity and their wide field of application. They are generally used for assembly or component insertion operations.
- ANTHROPOMORPHIC ROBOT: This robot has 3 positioning joints and simulates the movements of a human arm. The first axis corresponds to the arm, the second to the forearm and the third to the wrist. Within this type of robots, we find 5-axis, 6-axis and 7-axis robots. As for the latter, what differentiates it from the 6-axis one is that the base is mounted on a linear guide (track), which allows it to move forwards and backwards. This robot has great accessibility and manoeuvrability, it is fast and takes up little space with regards to the work field it covers. The integration of these robots is accompanied by specific security measures. They are used for welding, assembly, filler, paint and palletizing applications.
- COLLABORATIVE ROBOT or COBOT: Regarding this robot, we can say that it is an anthropomorphic robot, but of smaller dimensions and weight than those previously described. They are more manageable robots, easy to program and do not require specific protection measures. Due to its size, it allows it to load less volume of product and less weight. Furthermore, it’s slower than industrial robots. Nevertheless, they allow greater flexibility, since they can be easily transported from one phase of the process to another.
- AGVs (Automatic Guided Vehicle): We can identify these robots as autonomous vehicles with an applicability closely linked to the internal logistics of the company. They are also suitable for integrating a collaborative robot, which must move from one phase to another of the production process.
ROBOTICS IN HVET/VET LABS
The integration of robotics in the HVET Miguel Altuna is understood from three points of view:
1. Specific robotics laboratories
2. Integration of robotics in the advanced fabrication shop
3. Integration of robotics in the CLF
In the first case, we find the creation of a specific robotics workshop where we learn the basic knowledge necessary to be able to work with robots. To do this, problematic situations are created and posed to a class configured in teams, where the work process has to train students to experience the situation as a challenge and, from there, they must have the opportunity to generate the necessary knowledge to provide the best solutions.
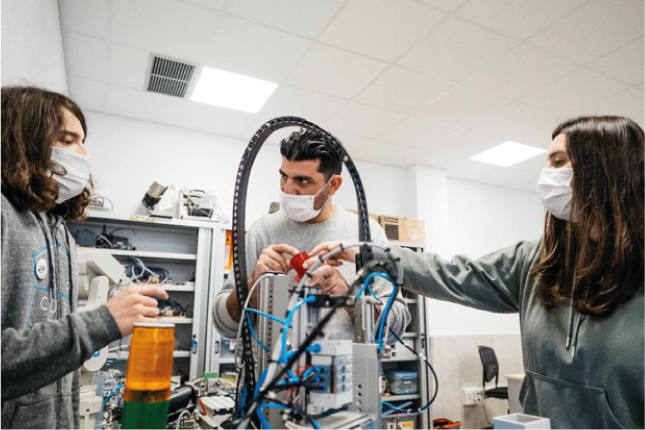
Figure 3: Students working on a project in Miguel Altuna Robotics Lab. Source: Miguel Altuna
This lab occupies an area of 130m2, in which 20 students, grouped in 5 islands, can work at the same time. The area of the lab is designed as a dynamic space where there are 20 stations, 4 robots (2 industrial and 2 collaborative), 2 artificial vision cameras and 6 frequency inverters that can be moved and grouped in different ways to simulate different real production processes. Each of the stations is governed by industrial automation (Siemens, Omron, etc.) and they are communicated with the rest of the stations through an industrial communications bus (Profibus, Ethernet, etc).
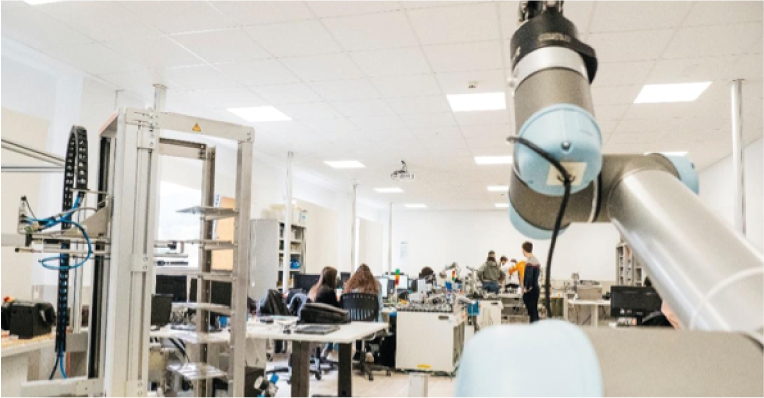
Figure 4: Miguel Altuna’s Robotics Lab. Source: Miguel Altuna
In the second stage, the objective is to transfer what has been learned in the robotics lab to the advanced manufacturing lab. To do this, an attempt is made to find possible needs that may exist in the workshop and a solution to those needs.
As practical cases of the school, the last two projects can be mentioned:
- Integration between 3D scanner and collaborative robot for industrial metrology
In this project the objective has been to automate an industrial process for its optimization.
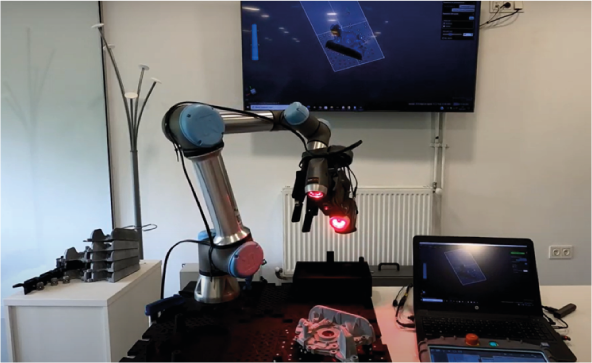
Figure 5: 3D scanner integrated in a collaborative robot. Source: HVET Miguel Altuna and HVET Tolosaldea
They have joined a 3D scanner with a collaborative robot and claws have been added to hold the pieces.
For more information: https://www.youtube.com/watch?v=zVxvvuvBc6o
- Create a robot that transports material in the workshop
The objective of this project was to integrate a MIR Robot in the manufacturing lab, simulating the functionalities that a MIR would have in an industrial environment. We worked on the communications and programming of the robot considering all the safety regulations.
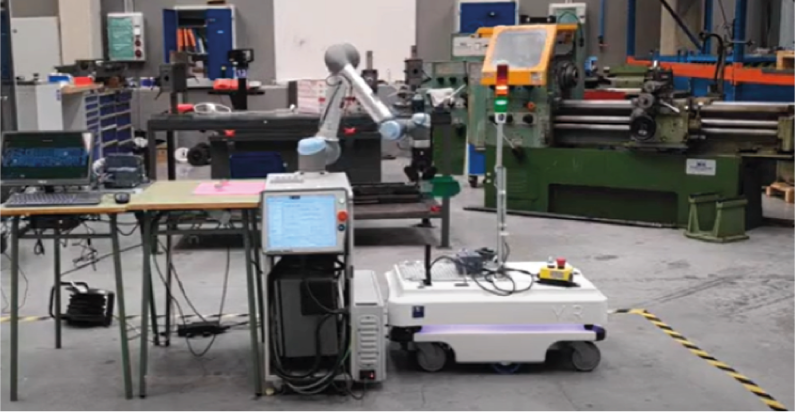
Figure 6: A MIR robot taking material from a warehouse with a collaborative robot. Source: Miguel Altuna
For this, a MIR robot is joined with a collaborative robot that has to be fitted with an RFID key to be able to call the elevator and move between floors.
More details: https://www.youtube.com/watch?v=s69xxGdPnaA
As a final phase, everything learned in the previous two phases would have to be used in order to improve a real industrial CLF process. The insertion and role of robotics in the CLF is detailed in the following sections.
- Create an autonomous MIR robot to transport material around the school
The last project is for a MIR robot to overcome obstacles such as elevators when transporting material through different parts of the school.
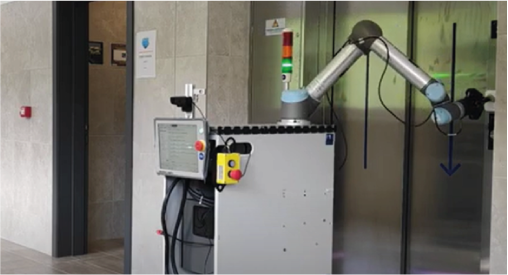
Figure 7: Robot calling to the elevator. Source: Miguel Altuna
For this, a MIR robot is joined with a collaborative robot that has to be fitted with an RFID key to be able to call the elevator and move between floors.
More details: https://www.youtube.com/watch?v=s69xxGdPnaA
As a final phase, everything learned in the previous two phases would have to be used in order to improve a real industrial CLF process. The insertion and role of robotics in the CLF is detailed in the following sections.
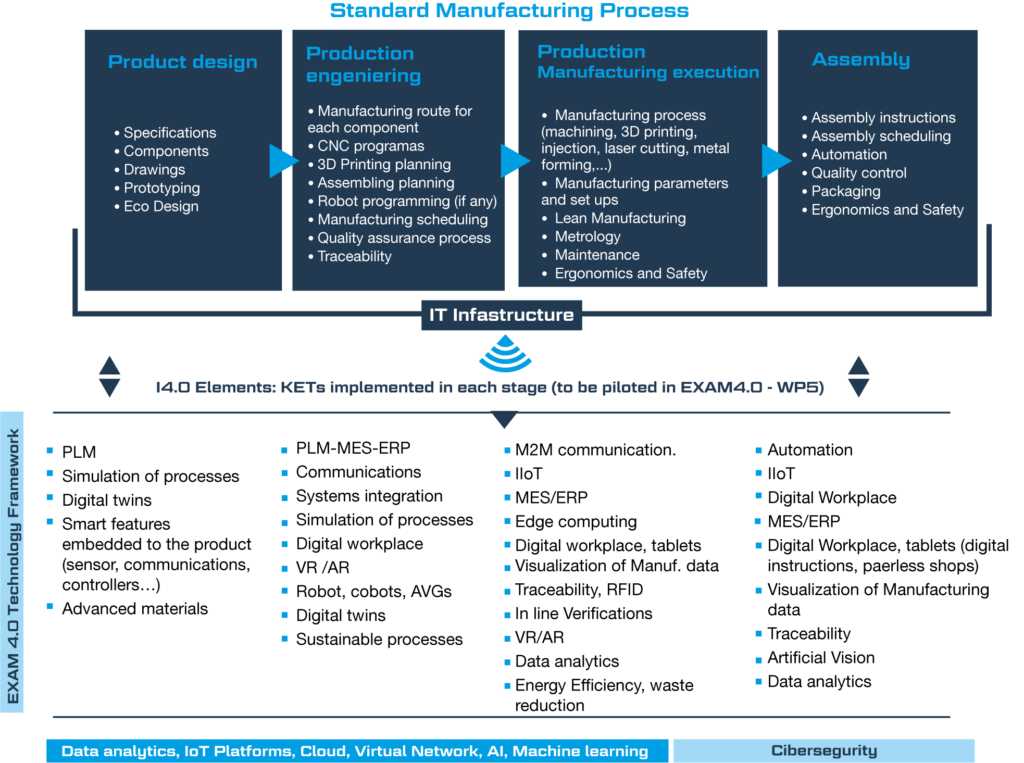
Figure 8: Exam 4.0 CLF value chain Source: Author’s creation
The main objective of the robotics in the production phase as well as in the assembly phase would be to optimize the entire process. For this reason, it would be interesting to incorporate the robots that have been mentioned above. The MIR with the collaborative could take care of the transport of the material and tool, eliminating or reducing the loss of time due to the movement of people or materials. Moreover collaborative robots could be incorporated in the quality phase, with a 3D scanner, or in the assembly phase, with different claws, to speed up repetitive work.
Finally, the product to be made at the CLF in this case has been a robot capable of moving around the workshop. The robot could serve either to move parts or material from one side to the other. This robot would be customizable, being able to add any new sensor or, as can be seen in the image, a collaborative robot.
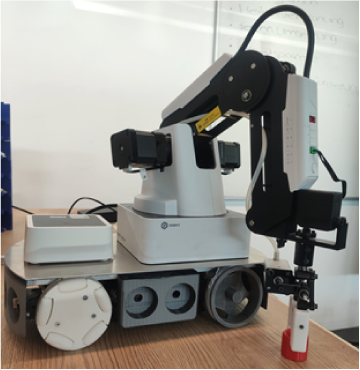
Figure 9: Exam4.0 robot in conjunction with a collaborative robot. Source: Author’s creation
The application of robotics in the CLF helps in the correct functioning of the manufacturing and assembly processes. Among the benefits of inserting robotics in EXAM CLF are:
- Cost reduction, promoting operational efficiency, reducing production and assembly costs.
- Automation of processes. The processes will become more and more automatic, avoiding errors of manual operators.
- Better monitoring by obtaining information (status, consumption, etc.) in real time.
- Maximum use of resources, making them more efficient.
- Increased safety as robots perform risky tasks.
The competences acquired with the robotics can be classified into two groups: Technical and soft competences.
The technical competences are the ones that are most closely related to the technical content to be acquired in the learning process of the students. The insertion of robotics is going to help in developing competences related to I 4.0such as:
- Configuration and programming of BCR, QR, Data matrix, RFID readers, etc.
- Configuration and programming of artificial vision cameras, mobile devices, tablets, etc.
- Identification through monitoring.
- Software virtualization. Virtual machine.
- Program monitoring.
- Robot programming (industrial / collaborative) with integrated vision.
- Data digitization and analysis.
- Internet of things, IoT.
- Cybersecurity in the industrial environment.
- Simulation of the process using a twin or mirror image.
- Data acquisition and monitoring locally and in the cloud.
Secondly, about the soft competences that are worked with ERP are:
- Teamwork: being a collaborative tool, team members can plan their tasks and all have access to the production sheets, the control sheets….
- Digital: they get used to virtual working environments, understanding the data obtained, managing it and drawing conclusions.
- Personal: autonomy, initiative, critical spirit, to be aware of the importance of good planning and to see how the decisions taken in the process affect them.
- Communication: between students, the one who plans the production with the one who executes it, being aware of the importance of the different explanations (verbal and written) that are given within the production process and that can help achieve a better result.
COLLABORATION OPPORTUNITIES OPENED BY ROBOTICS
In the same way that the robotics domain covers a wide spectrum of technologies (mentioned in section 1), the options for collaboration also vary according to the field of robotics to which we refer. In fact, one of the branches included in robotics is called collaborative robotics.
As a general idea from the point of view of vocational training centres we will mention 2 collaboration fields:
- Collaborative robotics.
- Virtualisation of robotics by means of digital twins.
As the name suggests, COBOTS are designed to work simultaneously with people. Their characteristics offer an important number of applications in industry and also in education. The challenge in our advanced manufacturing labs is to find specific applications where students perform joint tasks for manufacturing parts and using COBOTs. Some examples are: loading and unloading of parts on CNC machines, feeding systems and assembly operations on LFs etc.
Virtualisation technologies, and especially digital twins technologies, offer great opportunities in the field of robotics.
The generation of virtual models of robots or robotic lines enables us to deepen in the field of robotics without the dependence on physical equipment (robots). Reader can refer to the document “I4.0 technologies #6: Digital twins” for further info.
Besides that, the digital twins of robotics systems enable the easy exchange of information, data and training solutions among different institutions.