Following the piloting process of Advanced Manufacturing Labs for H/VET through the Collaborative Learning Factory (hereafter CLF), the EXAM4.0 partners we have piloted 16 technologies embedded in Industry 4.0.
The following image shows the overall structure of the piloting process.
Labs for Advanced Manufacturing-CLF
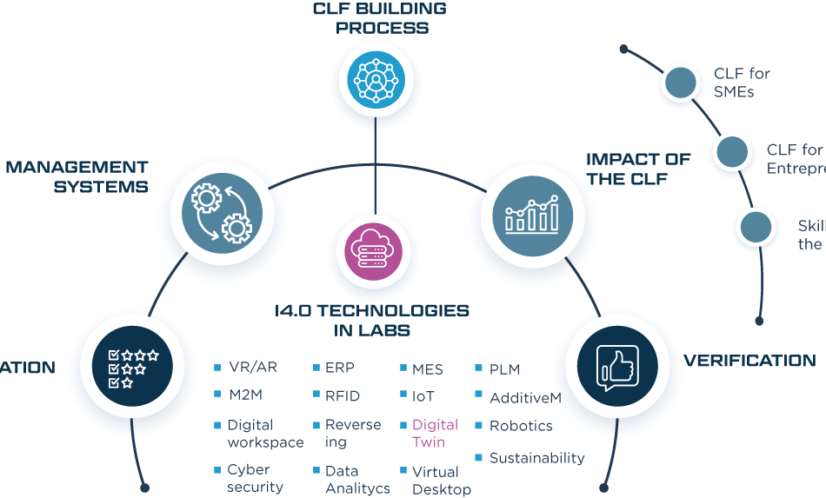
The present report is the one out of 16 I4.0 technology described within the “Industry 4.0 technologies in labs” section, specifically #6 Digital Twins.
DEFINITION AND APPLICATION OF DIGITAL TWIN IN INDUSTRY
A digital twin is a digital representation of a real-world entity or system. The implementation of a digital twin is an encapsulated software object or model that mirrors a unique physical object, process, organization, person or other abstraction. Data from multiple digital twins can be aggregated for a composite view across a number of real-world entities, such as a power plant or a city, and their related processes.
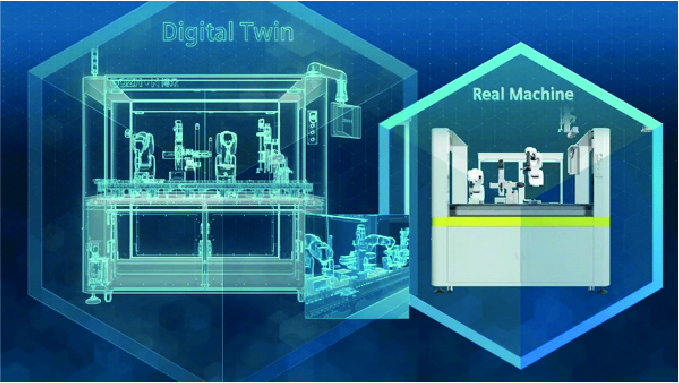
Figure 1: Digital twin in production. Source: https://www.plm.automation.siemens.com/global/es/webinar/digital-twin-in-manufacturing/68561
The digital twin concept consists of three distinct parts: the physical product, the digital/virtual product, and connections between the two products. The connection between the physical product and the digital/virtual product is data that flows from the physical product to the digital/virtual product and information that is available from the digital/virtual product to the physical environment.
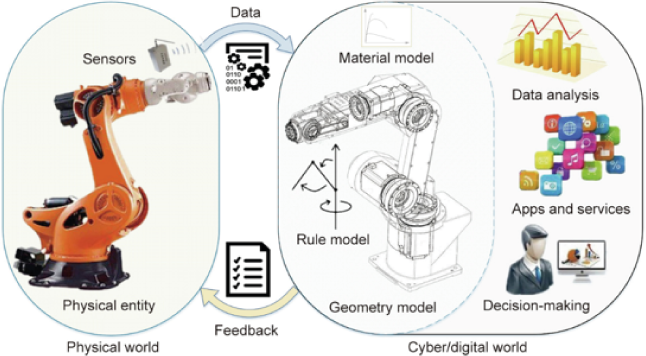
Figure 2: Digital twin architecture. Source: https://www.engineering.org.cn/en/10.1016/j.eng.2019.01.014
To create a digital twin, you have to collect a lot of data, both about the object and what is around it. With this information, computational models that represent the behaviours or states of the physical object can be created (Xataka, 2021).
This data can be related to the life cycle of a product, its design specifications, its production processes, engineering and production information (including materials, parts, methods and quality control) …
A digital twin can be as complex or as simple as needed. The amount of data you collect will also determine how accurately the digital model simulates the physical version.
Once all the data has been collected, it is used to create analytical models with which to predict the effects and behaviours of that object in the event of possible changes.
These simulations are generated taking into account issues such as engineering, physics, chemistry, statistics, machine learning, artificial intelligence, business logic or objectives. These models can be displayed through 3D renderings and augmented reality modelling.
The development and creation of a digital twin is used mainly for three main issues:
- Digital Twin Prototype (DTP): before creating a final physical product, a digital one is made to see what it would really look like and how it would behave.
- Digital Twin Instance (DTI): once a product has already been manufactured, the digital twin is used to test different scenarios of use with the virtual and not with the real one.
- Digital Twin Aggregate (DTA): Collects information from the above case to determine a product’s capabilities, run forecasts, and test operational parameters.
Through these three typical use cases, companies can predict different outcomes based on variable data, which helps determine where things need to go or how they work before they are physically implemented.
Some of the advantages of digital twins in the industry that we can highlight are:
- To have a realistic model to carry out all kinds of experiments without putting the replicated production system at risk.
- To design new scenarios and observe their behaviour when the variables that concern you are modified.
- To know when system failures will occur, allowing us to develop maintenance plans in advance.
- To evolve the production system in an agile and constant way, incorporating changes that improve productivity in a real way.
- To predict the expected result with reliable data.
DIGITAL TWIN IN HVET/VET LABS
As a professional in technical education, you are challenged daily to deliver the most engaging and relevant course you can. The need to keep up to date with the latest technology innovations, whilst managing the resources you have, can be difficult.
This, coupled with a growing demand for online learning and remote access from your students, can create accessibility challenges (Simumatik, 2021).
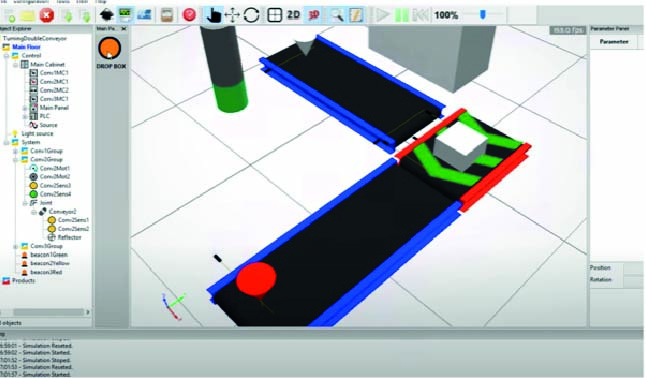
Figure 3: Working in Simumatik. Source: Tknika
Digital twins in education are particularly helpful. As mentioned earlier, they consist of virtual models of a process, product, or service, paired with its real-world counterpart. This pairing of the virtual and physical realms allows students to learn data analysis and system monitoring to avoid problems, as well as how to prevent downtime, develop new opportunities, and plan using simulations.
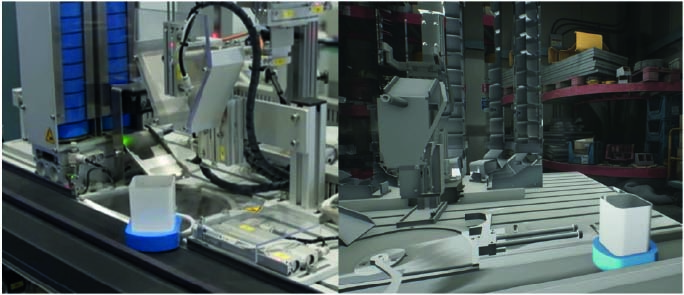
Figure 4: In the left the real machine and in the right the digital twin of the SMC SIF400 machine. Source: Tknika
One of the objectives of the Tknika digital twin workshop is to create a digital twin of the workshop equipment to allow the total simulation of processes of a real production process. The SIF-400 teaching team is working on this aspect, a SMC model that emulates a highly automated smart factory, including technologies related to Industry 4.0, advanced manufacturing concepts and the reality of the connected company.
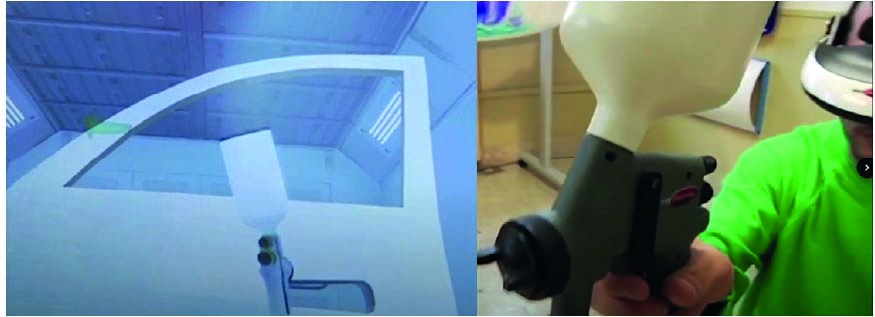
Figure 5: Student working on a car painting digital twin. Source: Tknika
Finally, digital twins of different individual production processes are being created so that students can practice in a digital environment, as long as they need production processes that would need a large infrastructure.
The digital twin in education enables:
- Students 24/7 access to a cloud-based resource.
- Digitizing physical labs.
- Putting key engineering concepts into practice.
- Collaborating on systems in real-time.
The CLF that is going to be launched has divided its production process into 4 stages (product design, process engineering, production and assembly) as can be seen in the following image.
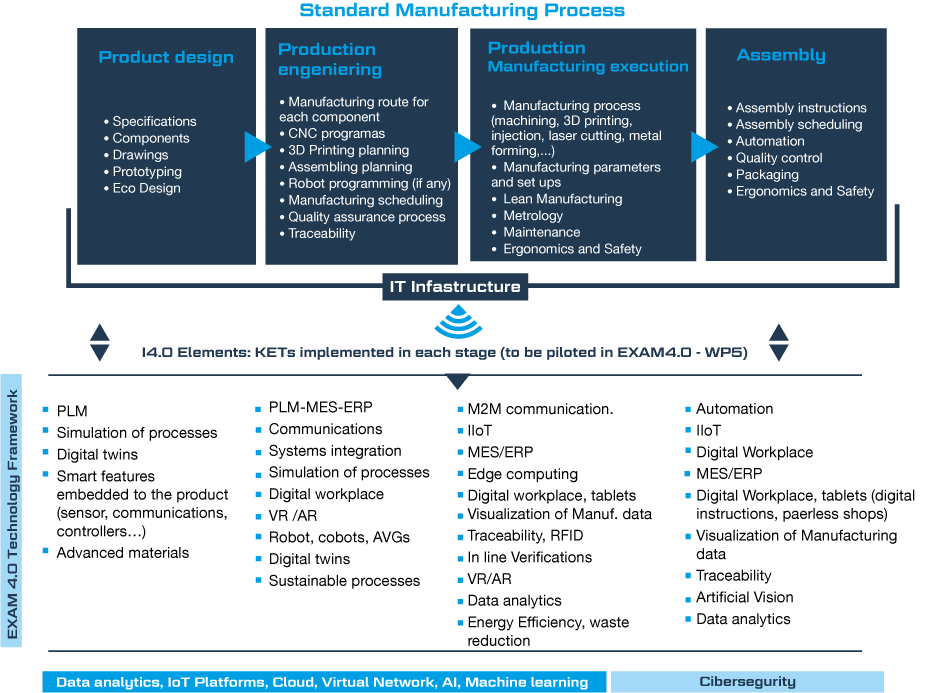
Figure 6: EXAM4.0 Collaborative Learning Factory’s (CLF) Value Chain Source: Author’s creation
The main role of the digital twin in EXAM 4.0 will be to have a virtual representation of the Collaborative Learning Factory process so that students can work in an Industry 4.0 environment.
To develop the virtual representation, in Tknika we have analysed various software that will allow us to build the digital twin of the Collaborative Learning Factory. Through them we will model the process, simulate it and we will be able to debug the programs that will be executed in the industrial controllers of the machines. This task is known as virtual commissioning.
The software packages that have been evaluated for these tasks have been the following:
- Industrial Controller Simulators: Siemens PLCSIM Advanced v3.0
- Robot Simulators: RoboDK
- Virtual commissioning software: Simumatik and Factory I/O
On the basis of this software, we have worked on the design of an online course. The objective has been to test the use of these tools to build industrial virtual environments with a group of teachers.
In the course, there has also been a demonstration of the digital twin with hardware in the loop configuration. This kind of configuration will allow us to run a real controller connected to the digital twin, so that it works as it would in reality, subjecting it to different contexts of conditions, shortening thus the development, validation and commissioning times of the controller in a safer, more flexible and economical way.
The benefits of having a virtual model of the CLF will be several:
- Avoid breakages, safety issues, and limitations for students by moving Collaborative Learning Factory Labs online.
- Virtual sharing of equipment and resources between different centres without the need to duplicate resources.
- Support key technical concepts and allow students to put theory into practice. Enhance student learning in the basic principles of physics, including electricity, pneumatics, and hydraulics.
- Support your own lessons with access to virtual labs and give students the ability to create their own.
The competencies addressed in Digital Twin vary depending on learning goals. However, following are examples of competencies addressed within the scope of Digital Twin in the EXAM 4.0 CLF:
- Prepare the control programs, in accordance with the specifications and functional characteristics of the installation.
- Define the assembly protocol, tests and guidelines for virtual commissioning of automatic installations, based on the specifications.
- Build purposeful and tailored representations of complex models and their related information.
- Create Digital Twins using 3D software.
- Run simulations to measure product performance in varying conditions.
- Adapt to new work situations caused by technological and organizational changes in production processes.
- Analyse and record the interactions.
- Visualise the results of interactions.
- Deliver the security that modern services demand.
COLLABORATION OPPORTUNITIES OPENED BY DIGITAL TWIN
Through the tools to create digital twins, a base of 3D models of machines and processes can be created in order to share them among the partners. The digital twin is a very valid tool in the field of training since it does not allow a total dependence on the equipment, making it more affordable for the centres to work on complex or very expensive aspects.
In addition, any participating centre that does not have sufficient resources to have all the machinery, will be able to work online using computers, virtual reality glasses … simulating real machines with data in real time. All this means that different centres that are in different countries can also be working at the same time through the aforementioned devices in a collaborative way.