Following the piloting process of Advanced Manufacturing Labs for H/VET through the Collaborative Learning Factory (hereafter CLF), the EXAM4.0 partners we have piloted 16 technologies embedded in Industry 4.0.
The following image shows the overall structure of the piloting process.
Labs for Advanced Manufacturing-CLF
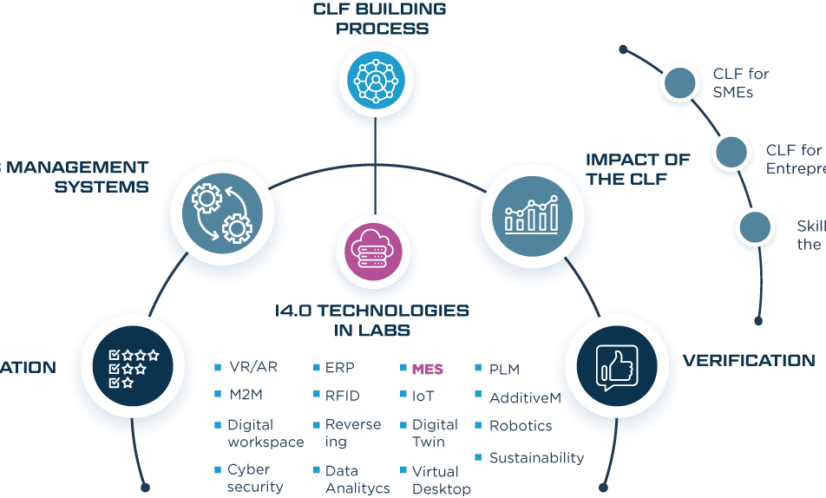
The present report is the one out of 16 I4.0 technology described within the “Industry 4.0 technologies in labs” section, specifically #15 Manufacturing Execution Systems (MES).
DEFINITION AND APPLICATION OF MES IN INDUSTRY
Manufacturing Execution Systems (MES), or also denominated Manufacturing Operations Management (MOM), are systems used in production to track and document the transformation of raw materials into finished products. MES works in real time by integrating plants or lines with equipment, controllers, operators to enable control of multiple elements of the production process (e.g. consumption, personnel, machines and support services).
MOM is a holistic solution that provides visibility into manufacturing processes in order to optimise efficiency. MOM consolidates quality management, planning and sequencing, production execution and other processes (Wikipedia, 2021).
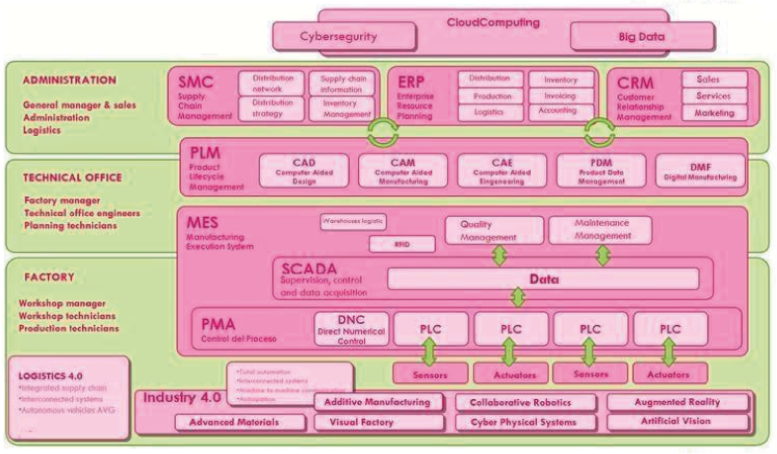
Figure 1: Integration of ERP-PLM-MES within the structure of the company. Source: Ibermatica
The MES system can operate across multiple function areas, for example: management of product definitions across the product life-cycle, resource scheduling, order execution and dispatch, production analysis and downtime management for overall equipment effectiveness (OEE), product quality or track and trace of materials. MES creates the “as-built” record, capturing the data, processes and outcomes of the manufacturing process.
Manufacturing processes are composed of a number of stages that must be coordinated. These stages require the careful coordination of material, resources and information to make and deliver the product efficiently.
The following is a generic list of the high-level processes within the scope of manufacturing (Vokey, 2020):
- Material procurement — When, how much, and from whom.
- Material receipt (including incoming inspection) and storage — Frequency of delivery, where to place the delivery once it is in-house, and verification of material quality.
- Material and product inventory management — All material movement within the plant.
- Production planning and scheduling — When to produce and how much, which includes sequencing the manufacturing processes for the product or subassembly at both the subassembly line level and the final assembly level.
- Maintenance and readiness of tooling and conveyance systems — Ongoing maintenance and calibration keeps the tooling and conveyance available when needed.
- Training and readiness of operators, supervisors, and other staff — Having both the knowledge to perform the work and the right skills when needed, in order to minimize costs.
- Product quality assurance — When tests should be performed on products or materials to check the product’s quality while reducing potential waste if anything goes wrong.
- Shipment scheduling and coordination — Ensure the product is shipped on time for delivery and minimize port fees.
The interaction of 3 main elements is essential to assure the coordination of every single element that takes part in the overall production: ERP-PLM-MES.
MES IN HVET/VET LABS
The implementation of a MES system requires that each of the machines that want to connect to the system can communicate with the software that has been chosen. The machines and equipment, through Wi-Fi communication, transmit all the data they have to a database located in the cloud through CNC.
In IMH lab, they have communicated the following workshops:
- All the CNC machines correspond to the TKGUNE workshop, whose objectives are to offer technological innovation services to SMEs and to be a training space for the 2 specialization programs in Industrial Mechatronics and in Mechanical Production Scheduling.
- All the CNC machines and, for now, 6 conventional machines by integrating PLCs to communicate with the MES, corresponding to the general workshop aiming at the development of the teaching-learning process of vocational training cycles.
It is important to clarify that when incorporating a MES in the workshops of vocational training centres, the information management and processing will be different from the way industry does. This is because the teaching-learning processes require a different management.
The available information concerning this lab is:
- Traceability of learners, machine usage, tools, performance indicators.
- Machine use information for scheduling, planning and also maintenance.
- Monitoring of student’s performance, state of project’s and task execution at real time.
- Tools control.
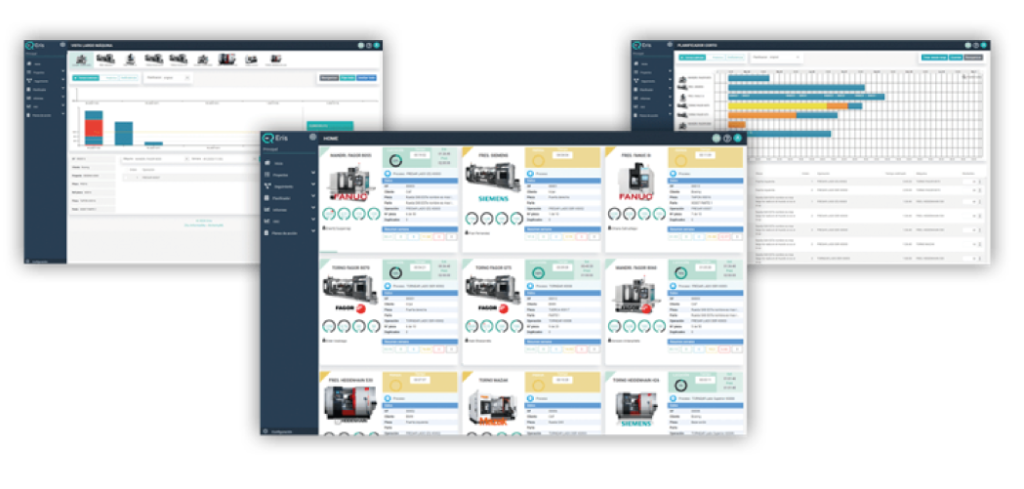
Figure 2: Monitoring of machine data Source: https://www.zitu.net/es/soluciones/eris
The CLF that is going to be launched has divided its production process into 4 stages (product design, process engineering, production and assembly) as can be seen in the following image. Within these stages, and taking into account the ERP-PLM-MES systems, the MES is going to work in process engineering, production manufacturing and assembly stages.
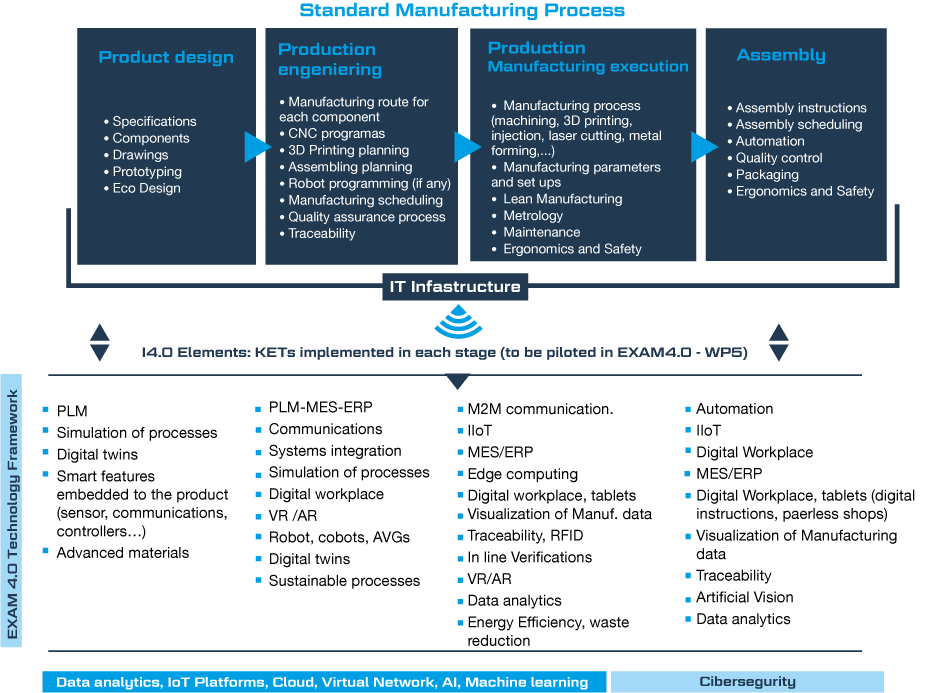
Figure 3: EXAM4.0 CLF value chain Source: Author’s creation
One of the objectives of the CLF is to be able to transfer data between labs in order to control the manufacturing process. For this purpose, in the labs, there are going to be some technologies and machines that connected with sensors would transfer data through PLCs to a MES. This MES would be connected to the technical office part through a PLM and to the administrative part through an ERP. All this data would be transferred to the cloud to be later processed, always taking cybersecurity into account.
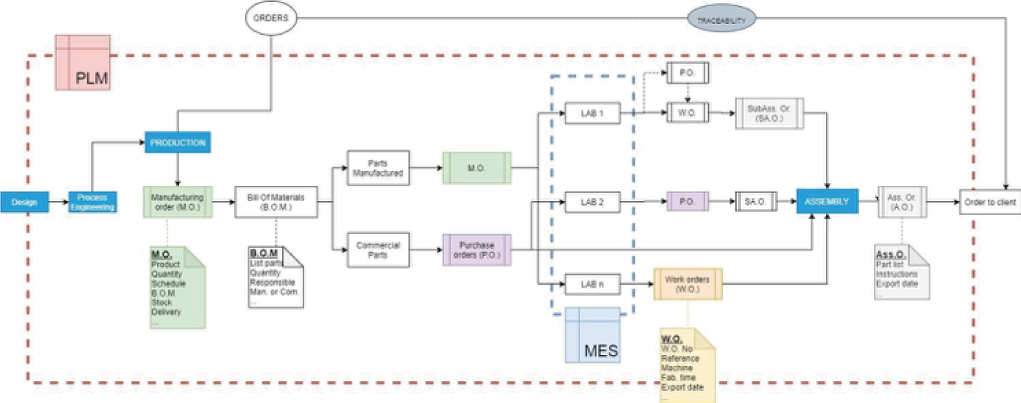
Figure 4: Diagram of the operation of the ERP-PLM-MES system of the CLF. Source: EXAM4.0
Taking into account all the production process, there must be a platform where orders can be placed. The order will reach an ERP. It is important that the ERP is common because the entire production process will be managed from there. Unlike ERP, the MES of each lab does not have to be the same, because it will be in charge of the operations of each lab. However, all MES will have to be able to collect and send the same information that is necessary for the common ERP.
Within the operations of the MES, on the one hand it will have to organize the resources once a manufacturing order has been sent. On the other hand, it will have to collect the necessary information in real time to be able to manage the ERP’s needs.
The application of a MES system in the CLF helps in the correct functioning of the process in general. Among the benefits of inserting MES in EXAM4.0 CLF are:
- Massive remote control managed through the use of applications. All machinery and equipment is visible at all times and in real time, being able to control operations and detect or solve problems.
- Cost reduction, promoting operational efficiency, reducing production and logistic costs.
- Automation of processes due to artificial intelligence. The processes will become more and more automatic, avoiding the errors of manual operators.
- Better monitoring by obtaining information (status, consumption, etc.) in real time.
- Maximum use of resources, making them more efficient.
The competencies acquired with the MES can be classified into two groups: Technical and soft competences.
The technical competences are the ones that are most closely related to the technical content to be acquired in the learning process of the students, in this case Machining Technicians, Mechanical Production Scheduling and Industrial Design. The insertion of MES elements are going to help in developing competences such as:
- Schedule productions, production planning, quality control and measurement procedures, maintenance planning.
- Prepare the procedures for the assembly and maintenance of equipment, defining the resources, the necessary times and the control systems.
- Supervise and/or execute the machining, assembly and maintenance processes, controlling the times and the quality of the results.
- Supervise the programming and tuning of numerical control machines, robots and manipulators for machining.
- Determine the necessary provisioning through an intelligent warehouse.
- Ensure that manufacturing processes conform to established procedures. Applied metrology.
- Manage the maintenance of resources in their area.
Secondly, about the soft competences that are worked with ERP are:
Teamwork: being a collaborative tool, team members can plan their tasks and all have access to production sheets, control sheets….
Digital: they get used to virtual working environments, understanding the data obtained, managing it and drawing conclusions.
Personal: autonomy, initiative, critical spirit, to be aware of the importance of good planning and to see how the decisions taken in the process affect them.
Communication: between students, the one who plans the production with the one who executes it, being aware of the importance of the different explanations (verbal and written) that are given within the production process and that can help achieve a better result.
COLLABORATION OPPORTUNITIES OPENED BY MES
As mentioned above, the interaction of 3 main technologies is essential to assure the coordination of every single element that takes part in the overall production: ERP-PLM-MES
The technology itself is not a collaborative facilitator but it is essential for the correct functioning of the ERP. On the one hand, it is the system that will give the necessary information about the production process in real time to the ERP (production, maintenance, stock, etc.). On the other hand, it is responsible for taking the orders from the ERP and distributing the tasks in the lab. That is why, with the combination of ERP, from the information it collects, it enables different production processes of different schools or countries to be known. In addition, through collaboration, these processes could be improved or new ones created.
On the other hand, schools that do not have as much machinery or technology, could make use of the data obtained to be able to make practical cases of the different production processes.
The flexibility of the system makes it easy for other schools and other productive processes to become part of it.