Following the piloting process of Advanced Manufacturing Labs for H/VET through the Collaborative Learning Factory (hereafter CLF), the EXAM4.0 partners we have piloted 16 technologies embedded in Industry 4.0.
The following image shows the overall structure of the piloting process.
Labs for Advanced Manufacturing-CLF
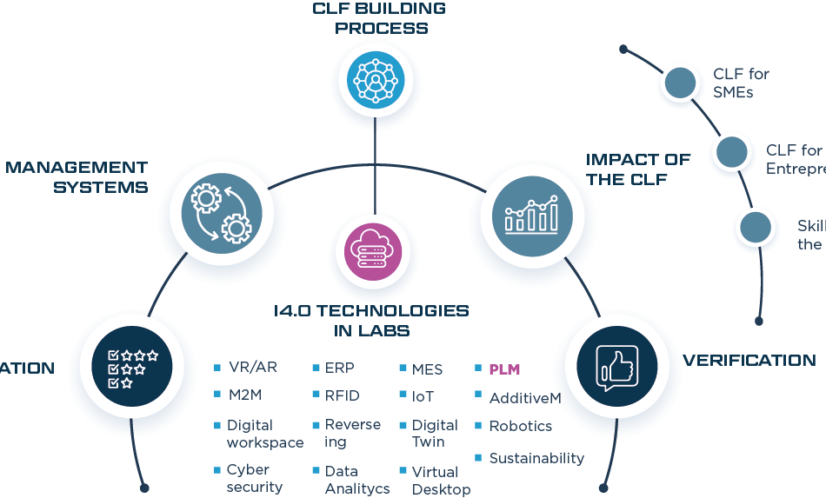
The present report is the one out of 16 I4.0 technology described within the “Industry 4.0 technologies in labs” section, specifically #13 Product Life Management (PLM)
DEFINITION AND APPLICATION OF PLM IN INDUSTRY
A PLM solution administers and manages the complete life cycle of a product. It promotes the final produc‘s digital definition in all its phases, starting with the conceptualization, going through the product design, the design of the manufacturing process, supply, manufacturing, distribution, after-sales (guarantees) and ending at the product end of life (Ibermática, 2021).
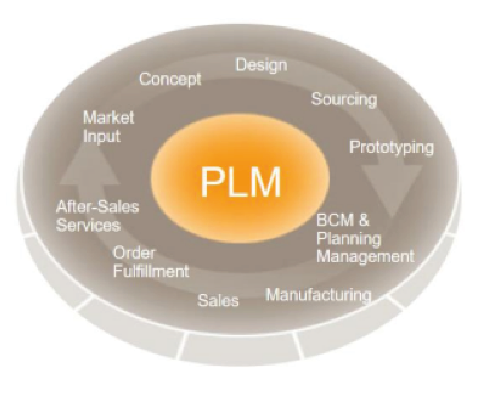
Figure 1: Phases of a PLM. Source: Ibermática
A PLM must integrate all the software solutions used for each of the previous stages, CAD solutions for design, CAE for analysis, CAM for manufacturing, PDM for product documentation management, ERP systems for production planning and production control or MES systems.
It manages all the information generated by each of the previous applications in a transparent way, ensuring the availability of specific information, at the right time, to the correct person.
In addition to data and information, a PLM can support all the processes that a company manages:
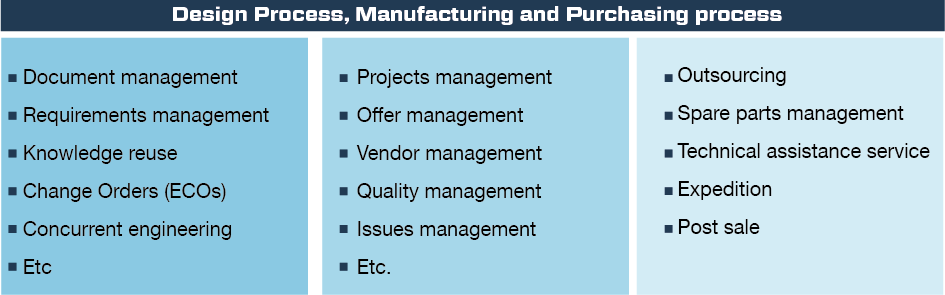
The PLM concept emerged in the beginning of the 80s of the past century, as a digitalization project of a small automobile company “The American Motor Corporation” (acquired in 1987 by Chrysler) for the development of the Jeep Grand Cherokee. Since then PLM has evolved from two different ways: From CAD systems and from ERP systems.
In the 3D CAD systems, the relationship of assemblies, components and drawings, the reuse of parts in different products and the need to manage product configurations, unleashed to the development of PDM (Product Data Management) systems, both for data management and product documents. These PDM systems evolved to encompass other company software programs and processes, giving rise to PLMs such as Enovia PLM (Dassault systems), Siemens PLM (Siemens) or Windchild PLM (PTC) to give a few examples.
ERP systems were created for production planning, and evolved to manage more and more processes, adding document managers and PIM (Product Information Management) capabilities to reach current systems such as SAP PLM or ORACLE PLM CLOUD to name a few.
The PLM systems are aimed at product manufacturing companies, rather than distribution companies or service companies.
The higher the variability of products that a company manages and the more important the design factor is, the higher advantage it will obtain in the use of a PLM system. Because of this, ETO (Engineering to Order) companies have been the first to adopt this type of technology.
Product Life Cycle Management (PLM) is a fundamental enabler in any company that wants to tackle a Digital Transformation.
The Products are increasingly complex and the suppliers are more global and geographically distributed. A PLM drives and automates digital processes inside and outside of these companies, improving communication, collaboration and control of transactions with these providers.
A PLM provides flexibility for the organization and allows the optimization of the daily activity of each of the phases of the product development. This flexibility increases the capacity for innovation, both in products and in manufacturing processes.
A PLM will improve productivity, since it facilitates the automation of the management of product data and its integration with other business processes such as ERP for production planning and MES systems for manufacturing execution management.
A PLM avoids information silos that exist in companies due to the use of specific tools for specific processes not integrated between them. This ability to integrate all the relevant information of a product allows companies to make better and more informed decisions.
Industry 4.0 defines new technologies and manufacturing methods.
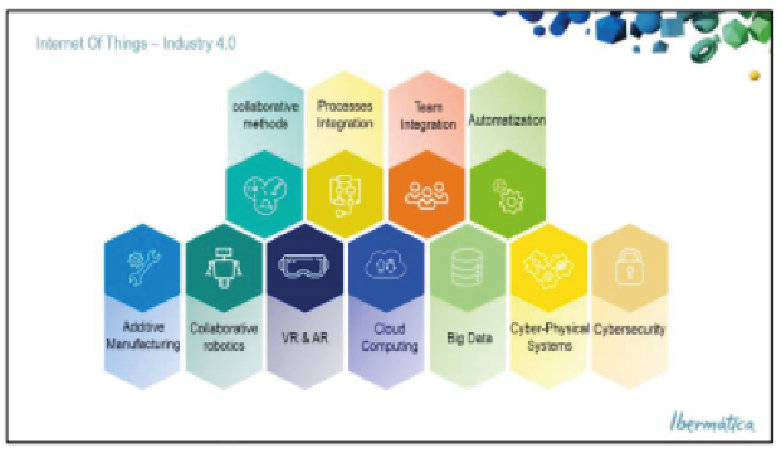
Figure 2: Industry 4.0 technology. Source: Ibermática
Collaborative methods, critical to achieving distributed manufacturing, process integration, and automation, are perfectly modelled in PLM systems.
On the other hand, technologies such as Digital twin or Big Data for data analytics need PLM systems for their support and exploitation.
The main evolution of the PLM systems is their transformation from being interconnected software tools to becoming systems that provide data services. They have gone from being a data repository to being a source of information exploitation.
These highly personalized software tools, programmed to suit the client and installed in complex hardware architectures, are evolving to more standard systems (out-of-the-box) simply configured, integrated and installed in outsourced or external hardware servers.
The access to tools, and consequently to their data, has gone from being departmental, to allowing global access.
The most current PLM systems are developed through open architectures (web services and so), which allow, beyond the exchange of data between applications, to add new capabilities to connect processes.
The high acquisition cost of PLM systems has been the main reason why only large companies have implemented these systems. The evolution of PLM towards SaaS systems (Software as a Service) with a pay per use, together with the outsourcing of the infrastructure, has allowed its expansion in small and medium-sized companies.
Another fundamental factor in the evolution of PLM systems is in the communication models they use, they have gone from sending messages and notifications to using current communication models based on social networks. A modern PLM will create communities to socialize, communicate, encourage participation, get feedback, etc.
To support the evolution of PLM systems, new collaboration platforms emerge. They are virtual workspaces, which centralize all the functionalities of a PLM, that is, the software tools, the information, the data and all the work processes defined by the organization.
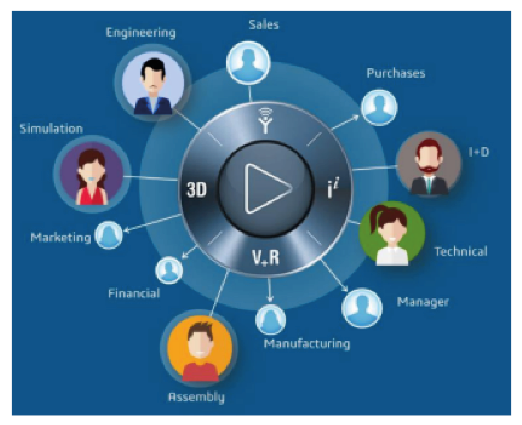
Figure 3: PLM as a collaboration platform. Source: Ibermática
This centralization allows simplifying access through a single point of entry, to all functionalities, measuring the degree of use to rationalize it and obtain process metrics.
The main objective of the platforms is to promote collaborative tasks, optimize communication and team coordination.
The collaboration platforms are generally developed on cloud servers, accessible through internet browsers to guarantee access to them from anywhere, at any time and from any device.
The main obstacle of implementing a PLM in the cloud is the security. The main fear is that confidential data could be compromised, having to protect both physical access to them and unauthorized access to data. The recovery of accidentally deleted data should also be ensured.
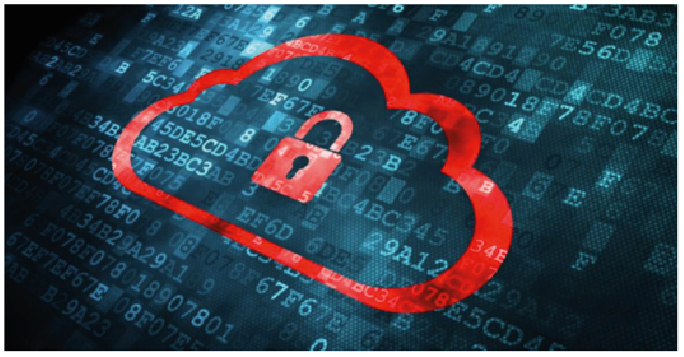
Figure 4: Cybersecurity. Source: Dassault Systémes
Access protection
In a cloud PLM, the servers are only accessible to very few people and with strict security measures. It is one of the main differences with an industrial company. In small companies, the availability of security personnel is limited. Large software development companies must protect their customers’ and their own data (and they only generate data) and invest many resources to guarantee it. Therefore, most companies can delegate security to the resources of these large companies.
Consistency & Data Security
The information access permissions limit the ability of any user to accidentally delete or modify information. Any access to the information is registered and stored in the history of accesses (log files) and actions carried out, being able to recover any previous state in a simple way.
In addition, the cloning of information on multiple servers and the available backup services offered by the PLM systems in the cloud, guarantee the recovery of the information in the event of any catastrophe.
Less and less backup copies are made and every day it is more common to make a “backup in the cloud” of the personal data and documents that we store to guarantee their persistence. Who does not save their cell phone photos in Dropbox, Google drive or a similar service?
Confidentiality of the information
In addition to the physical protection mentioned above, all the information housed in a PLM system is protected by the user access permissions. A user will only access the information which they are authorized to and a record will be kept of all accesses that have been made to obtain a complete traceability of the use of this information.
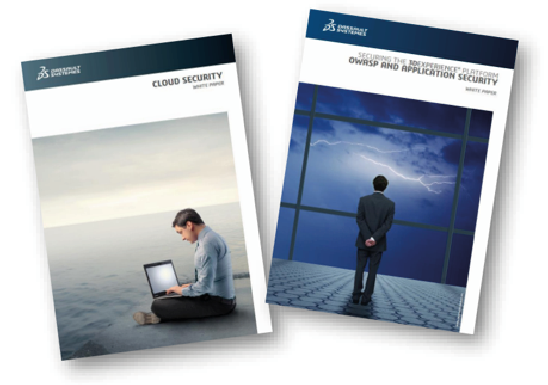
Figure 5: Dassault Systemes security documents. Source: Ibermática
Dassault Systemes security documents downloadable at:
https://www.3ds.com/products-services/3dexperience/resources/whitepapers/
PLM IN HVET/VET LABS
When implementing 3DEXPERIENCE, the following things must be taken into account:
It is necessary to define a long-term vision and involve the entire organization in the need for a digital transformation and the objectives to be obtained. If the users are not participants in the objectives to get, they will not perform the tasks that are added to their usual responsibilities.
The continuous communication of project progress and milestones achieved will be critical during the adoption of a PLM system.
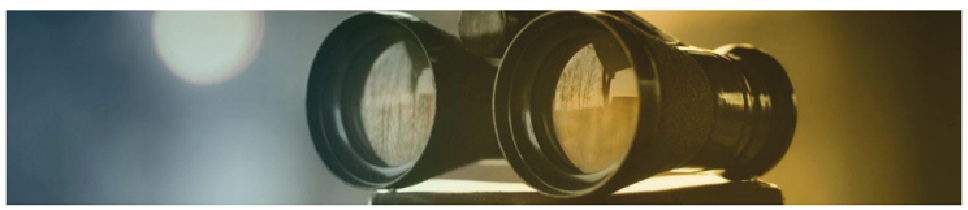
Figure 6: Long-term vision. Source: Ibermática
It will be necessary to involve the management team, appoint a project leader and prioritize those departments or processes in which the benefit is clear with the use of the PLM system. It will be better to start with a small project, with a specific objective and gradually expand it.
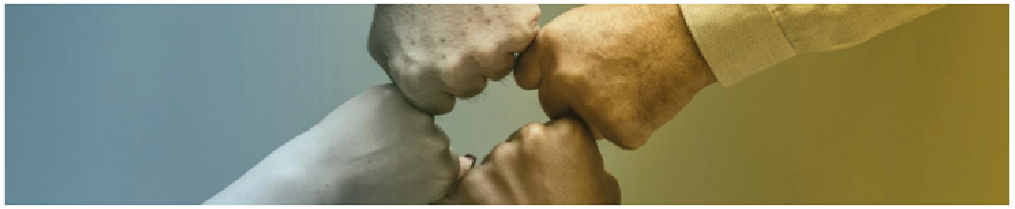
Figure 6: Involvement. Source: Ibermática
The chief of each department will be involved in the change process. They should be prepared for the possibility of change, by involving them in the process as soon as possible, asking them what their goals are about the system, and considering their opinions. This will facilitate the acceptance of the system and the success of the project.
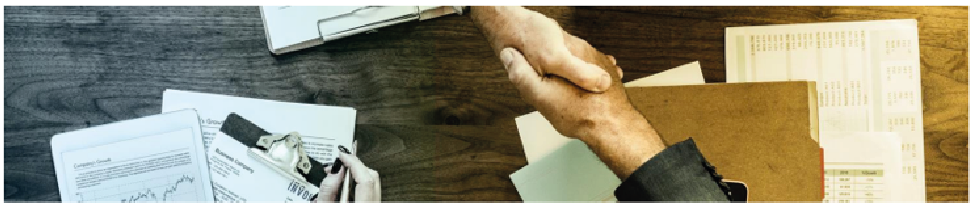
Figure 7: Involvement. Source: Ibermática
On the other hand, it is necessary to meet some requirements:
It will be necessary to carry out an analysis of the current situation of the company, for the review of existing processes and obtain metrics in order to quantify the expected improvement.
A PLM system implementation requires the participation of many people with different responsibilities and interests, which often leads to disagreements. It will be necessary to define the different roles and assign their main competencies. Minimally, it will be necessary to define the following:
- Responsible for PLM system implementation. Who shall be responsible for maintaining the long-term vision and responsible for the success of the implementation by not only having a technological focus, but also a strategic one.
- Functional manager. There should be one per department involved. They are responsible for setting specific objectives and proposing modifications to current processes.
- Systems manager. Who shall be responsible for guaranteeing the intellectual property of current systems through the correct integration of the PLM with existing systems.
- Economic manager. Who shall be responsible for ensuring the return on investment within the established period.
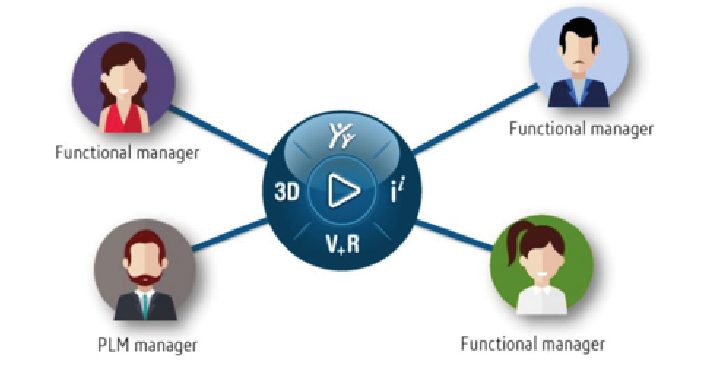
Figure 8: Team roles. Source: Ibermática
The scope of the global project and the different phases in which it consists must be defined. For each of the phases you must:
- Define a specific, limited objective that solves a real problem.
- Identify the minimum implementation that solves the problem.
- Define simple milestones and try to get them.
- Measure the improvement with the metrics extracted during analysis.
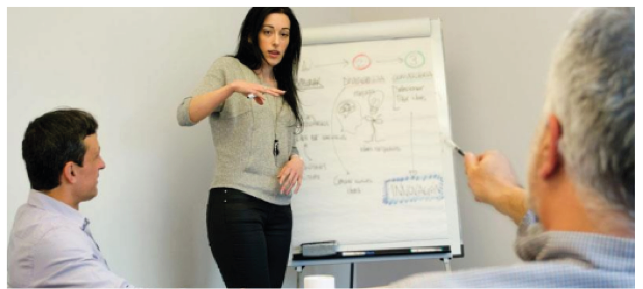
Figure 9: Planning the implementation process. Source: Ibermática
A fundamental aspect in the adoption of a PLM system is the involvement of users. They should not limit themselves to knowing the use of a PLM system, but must know it in the context of their daily work and this type of knowledge is not acquired in training courses. This approach requires an additional and specific effort for each type of user.
The ongoing support for technological changes should also be planned, by appointing experts within the team or by using the technical support service of the PLM system provider.
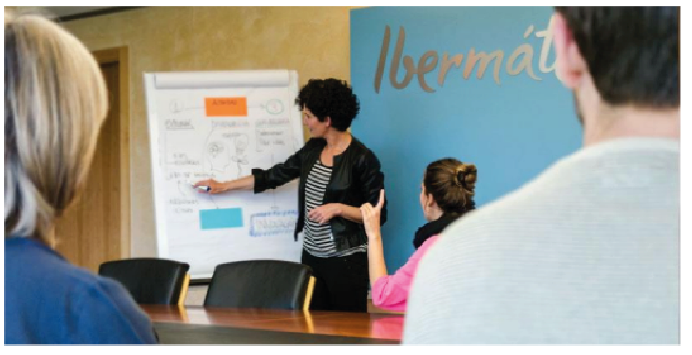
Figure 10: User training. Source: Ibermática
It is one of the key factors in the implantation process. There are two different approaches: to do a gradual migration of the information from the old systems to the new one or to carry out a massive migration of data during implantation.
In the first case, the systems coexist in time, leaving gradually the old one as a data repository as the use of the new system increases. In the second case, custom development is necessary. It is necessary to analyse the source data, its organization and its structure to be able to develop a migration tool. Although there is more and more development in this regard, they are still in a premature state.
In addition to PLM systems, executing product development processes require information from many different data sources and applications, ranging from 3D design (CAD), simulation (CAE), manufacturing (CAM), production management (ERP), manufacturing execution systems (MES), and a variety of in-house custom spreadsheets and databases.
The integration between these business systems is a natural step in any digital transformation initiative and it is fundamental in Industry 4.0. It allows users to access any information through a single centralized system. It will be necessary to:
- Identify the source where the data is generated.
- Determine what other systems require that data.
- Maintain a simple integration to share data between systems
- Review integration needs periodically
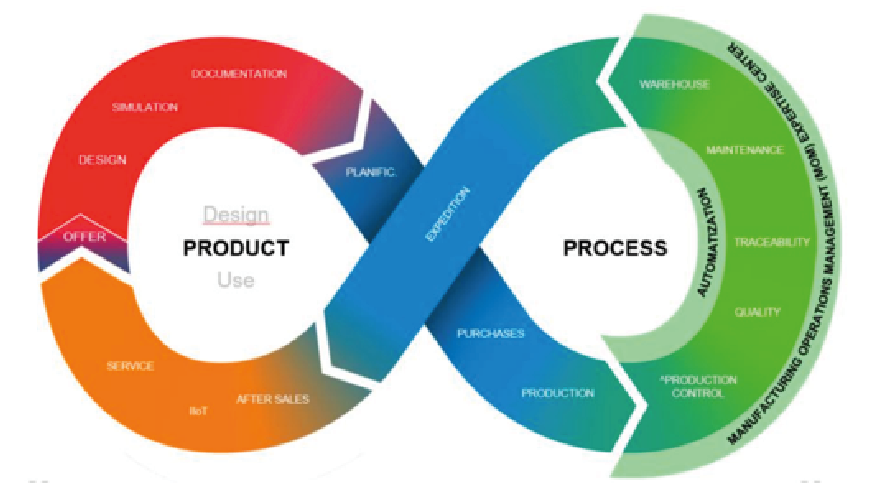
Figure 11: Integration of PLM with other systems. Source: Ibermática
The integration of the 3D parts with the articles, the bills of materials with the manufacturing structures of an ERP and the integration of the manufacturing operations of the articles with the MES systems, report benefits to each department.
The integration allows parts, assemblies, and drawings to be automatically coded based on a single company criterion.
It allows the engineering department to know the status of purchase or manufacture of a component or the expected delivery date to measure the impact of a design modification. It allows us to know the history of a part, the issues it has had and the maintenance information to consider them in subsequent redesigns.
The design engineer can know the stock of raw material and commercial components that are in the warehouse, choose the available material and commercial components knowing the price and availability instantly.
The items and the build structures are created automatically in the ERP from the design. The quantities of raw material required are automatically calculated from the engineering models. The mistakes made when entering them manually are avoided.
All documents are automatically associated with the article for viewing and consultation, ensuring that the correct version is always available.
Manufacturing operations are generated from CAM systems, estimating process times and productivity.
The documents of the ERP article are associated with each phase and operation, being available for viewing on the production plant. When you select a work order, the drawings, assembly instructions, and all associated documents are displayed.
The inspection dimensions read from 3D models create inspection guidelines for quality control automatically.
There may be some deployment risks:
- Not defining a long-term vision.
- Non involvement of the entire company from the beginning, or consider their opinions, even if the initial scope is limited.
- To start without defining specific objectives and continue forward, even if they have not been met.
- To start without understanding the current processes of the company, or without obtaining metrics from them.
- To not assign a person responsible for the implementation, and do not assign responsibilities to the team.
- To define a complete, complex and long planning, without defining control milestones.
- To not train users or train them only in the tool and not in the use of the tool in their daily work.
- To not consider data migration.
- To not analyse the integration with other information systems.
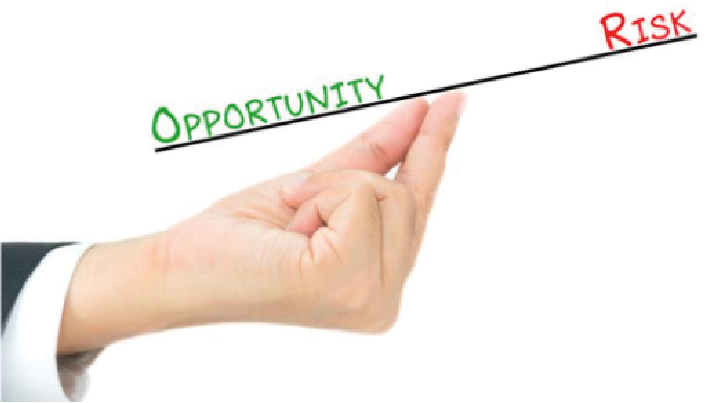
Figure 12: Opportunities against risks. Source: Ibermática
Talking about the platform, 3DEXPERIENCE on the Cloud provides all organizations with a holistic real-time vision of their business activity and ecosystem, connecting people, ideas, data and solutions in a single collaborative and interactive environment available at all times.
The easy-to-use interface helps everyone involved in innovation projects interact to imagine, design, simulate and deliver differentiated customer experiences. Break free of IT constraints to scale and ramp up faster than ever with the 3DEXPERIENCE on the Cloud.
More info at:
https://www.3ds.com/3dexperience/cloud
On the other side, Dassault Systèmes is a French software manufacturer specialized in 3D design, 3D digital mockups and solutions for Product Life Cycle Management (PLM). It has more than 20,000 employees of 140 nationalities.
It was created in 1981 for the digital transformation of aircraft design. Dassault Systèmes, based on the idea of “world virtualization”, has expanded its activity in the development and commercialization of professional software for all fields.
More info at:
https://www.3ds.com/about-3ds/
Referring to industry, Dassault Systèmes offers software solutions that enable customers to create new and innovative products through virtual experiences specific to each of the following industries:
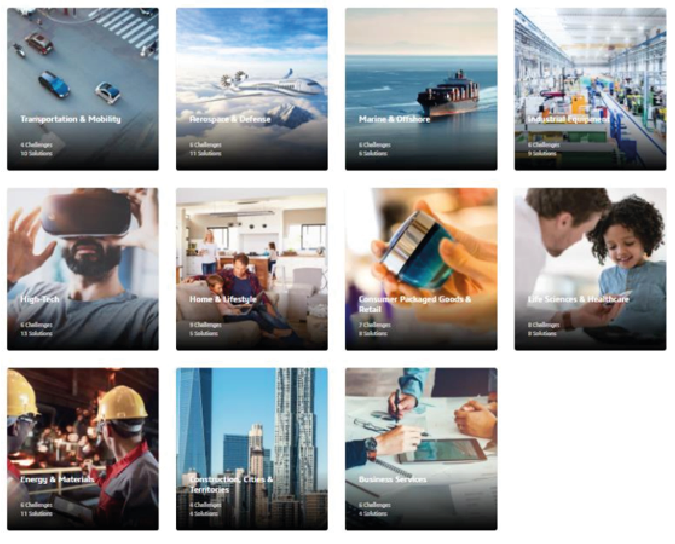
Figure 13: Industries where Dassault Systèmes offers a solution. Source: Ibermática
Inside these industries the platform works in different disciplines for Industrial Equipment. The 3DEXPERIENCE platform solutions portfolio for industrial equipment provides an organization with a seamless and collaborative product development environment in the cloud.

Figure 14: Disciplines for Industrial Equipment. Source: Ibermática
The 3DEXPERIENCE platform product development solutions help designers and engineers alike conceptualize, create, validate, communicate, manage and transform their innovative ideas into great product designs, managing all the different facets of the product life cycle.
Manage the end-to-end product development from early planning through development and final release.
To meet the increasing demands of higher quality, lower cost, and shorter product cycles, 3DEXPERIENCE platform provides a proven cross-industry backbone for your every product development need.
Collaboration and governance tools provide efficient and reliable processes to involve the right people at the right time, regardless if they are part of your company or are suppliers or customers. The design work from your favourite CAD is seamlessly integrated and execution of projects with elaborate dependencies across multiple teams has never been easier.

Figure 15: Governance. Source: Ibermática
Great products start with great design, but even the most innovative ideas will fail if they can’t be manufactured efficiently. What is required is a set of tools that enable identification of potential manufacturability issues that can be resolved earlier in the process. DELMIA Manufacturing & Production solutions allow businesses to operate in an ever-evolving world. This is accomplished by connecting all stakeholders to improve visibility into the design, manufacturing operations, and production. The result is improved agility and expanded continuous improvement across the enterprise. By providing a model-based, data-driven digital user experience, customers can establish a standard set of operational processes that can be created, managed, and governed holistically across an organization.
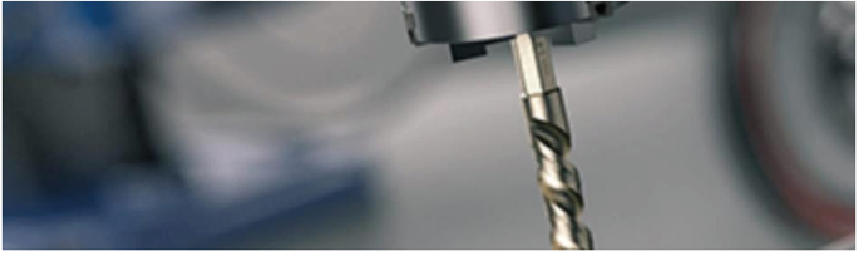
Figure 16: Manufacturing. Source: Ibermática
The 3DEXPERIENCE platform marketing solutions enable you to engage with customers and the market in a realistic way to understand what a product will look like in its environmental context. All project stakeholders are kept informed throughout the collateral development process with up-to-date information from a “single source of truth”.
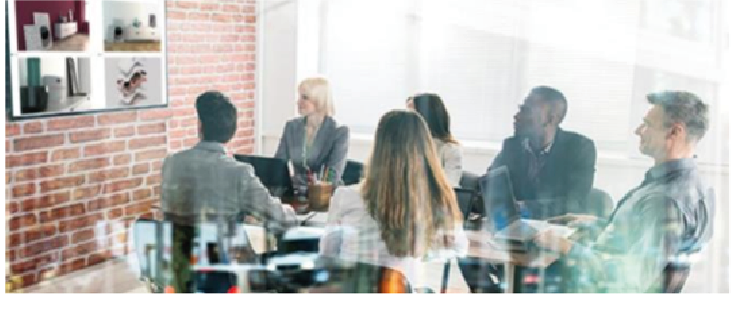
Figure 17: Marketing. Source: Ibermática
The 3DEXPERIENCE platform offers an integrated suite of simulation tools that accelerate the process of evaluating and improving product performance, reliability and safety before committing to costly and time-consuming physical prototypes. With market-leading simulation applications, our customers can meet their business goals of reduced cost and time to market while delivering innovative products.
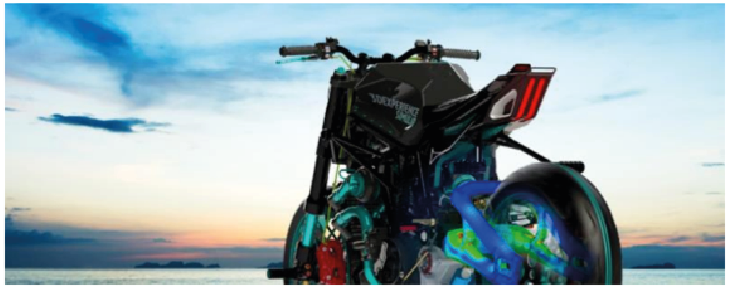
Figure 18: Simulation. Source: Ibermática
ROLE OF THE 3DEXPERIENCE PLM IN THE EXAM4.0 CLF
The CLF that is going to be launched has divided its production process into 4 stages (product design, process engineering, production and assembly) as can be seen in the following image. Within these stages, and taking into account the ERP-PLM-MES systems, the MES is going to work in the process engineering stage.
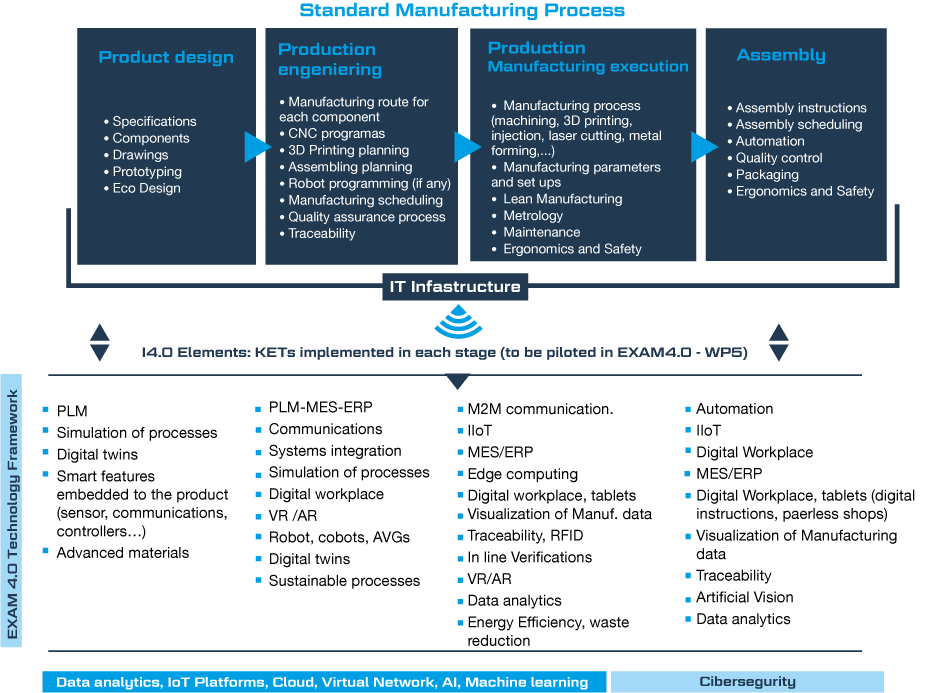
Figure 19: EXAM4.0 CLF value chain. Source: Author’s creation
A learning factory is a learning environment where processes and technologies are based on a real industrial site which allows a direct approach to the product creation process. Learning factories are based on a didactical concept emphasizing experimental and problem-based learning. The continuous improvement philosophy is facilitated by own actions and interactive involvement of the participants. (Reference: Laperrière& Reinhart: CIRP Encyclopedia of Production Engineering, 2015)
A product is designed, produced and assembled in different locations, following the LFs principles, i.e. in a learning environment where processes and technologies are based on a real industrial site. The co-creation process is based on continuous data & information exchange, a fully collaborative approach.
Although the most important applications of the 3DEXPERIENCE platform, in an engineering environment, are those that support its design and information management (PLM), as described in section 4, the 3DEXPERIENCE platform is an “ecosystem that connects people, ideas, information and applications in a single collaborative environment”. It perfectly fulfils the requirements of the “continuous exchange of data and information, in a totally collaborative approach” of the CLF.
It can support the different communication interfaces between LABs, through the most basic 3DEXPERIENCE applications such as:
- Virtualization of LABs: No need to maintain a physical location.
- Communication: Communities, Wikis, Notifications, Virtual meetings (audio, video), etc.
- Data repository: Data exchange / information sharing.
- Collaborative Tasks: project Gant, task assignment, activity control, task status, etc.
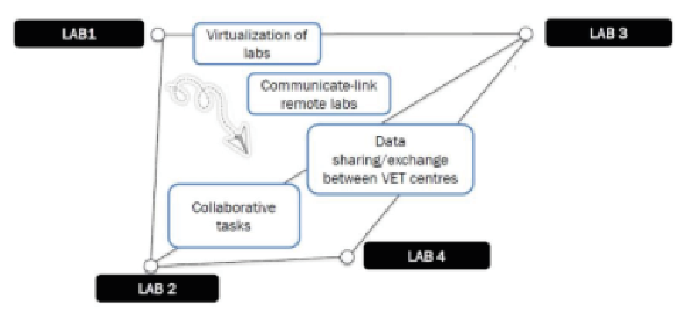
Figure 20: Communication between LABs in Exam 4.0. Source: Author’s creation
The 3DEXPERIENCE platform is, in turn, an application integrator, in addition to the platform itself, it has connectors for third-party applications: Catia, NX, SolidEdge, Inventor, etc. in the engineering area, up to iPaaS (Integration Platform as a Service) integration tools with ERP systems such as SAP or ORACLE.
3DEXPERIENCE functions in the CLF will be:
The most basic roles of the 3DEXPERIENCE platform provide users with all communication and collaboration capabilities, spaces to share information, and document viewers in the cloud.
In addition, it has tools for the communication of ideas: possibility of making 3D sketches, presentation of ideas, etc.
The role of product life cycle management (PLM) in the cloud, in addition to adding all the communication and collaboration functionalities, add capabilities such as:
- Revisions Management
- Document Management. States of maturity.
- Workflows
- Product structure management (BOMs)
- Issues Management
- Engineering changes management
- Projects management
- Task management
- Others
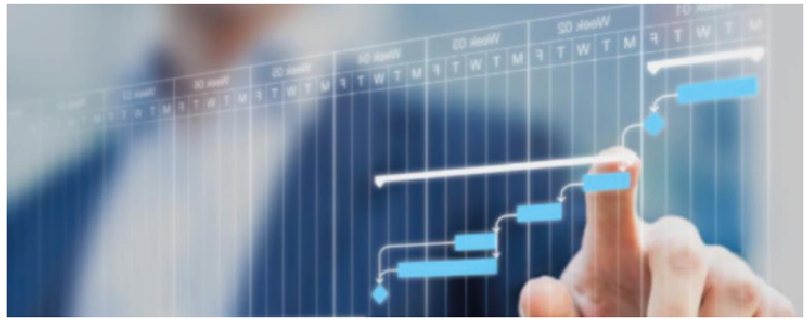
Figure 21: PLM planification. Source: Ibermática
EngineeringIn:
addition to connectors with most CAD / CAE systems on the market, the 3DEXPERIENCE platform has roles with 3D modelling applications in the cloud. It can also work natively with CATIA and SolidWorks for design and with SIMULIA for simulation in the cloud.
Functions extension:
There are many roles within the 3DEXPERIENCE platform that can add functions to the CLF, such as:
- CNC programming
- Digital Twins
- Simulation of manufacturing processes
- Virtual reality, augmented reality
- Others
An important function of the platform is that it can also be used as a training tool in addition to the CLF support tool.
BENEFITS OF USING 3DEXPERIENCE PLM IN EXAM4.0’S CLF
The application of a PLM system in the CLF helps in the correct functioning of the process in general. Among the benefits that inserting MES in EXAM CLF can have are:
- Functions extension
With a PLM system, all relevant information of the entire product life cycle is centralized. This centralization allows extending participation in it to suppliers and customers and in general to anyone outside the company.
The cloud-based PLM systems take this centralized access to data one-step further: The classification of information by function, process or department, adding the ability to access it from any web browser (without having to install any application), anyone can participate in a review, immediately and without any information exchange.
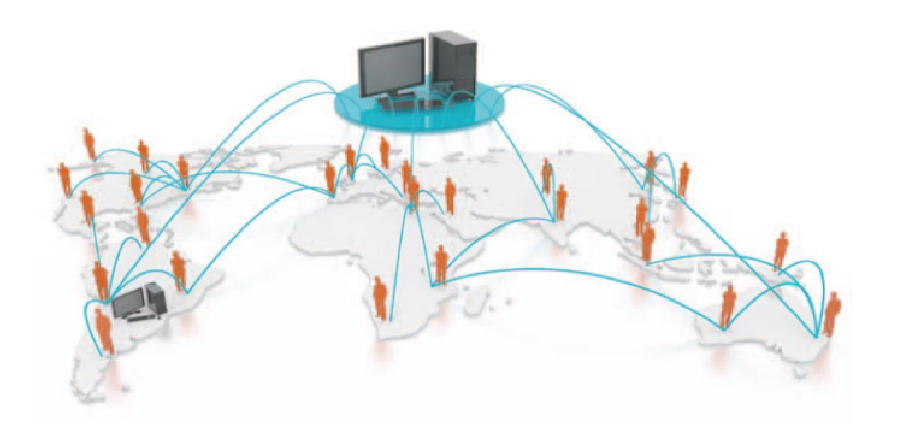
Figure 22: Centralization of the product life cycle. Source: Ibermática
- Offshoring
The access through any web browser, without requiring VPN connections to the servers, allows delocalized access.
- Expandability
A cloud PLM solution is inherently scalable. Adding a user (or several) to the system is as easy as typing their name. Unlike traditional PLM systems, there is no need to reconfigure the system, licenses, or download new releases. The new user simply logs in and has access to the system.
- Simplified maintenance
The IT department will be the biggest beneficiary of a move to the cloud. The process of installation, configuration and updating of traditional PLM systems is laborious and the update of each application must be reviewed with the rest to ensure its integrity, being common to clone the implementations for the realization of “tests”. With a PLM in the cloud, maintenance is outdated; updtes are automatic and managed by the same platform, guaranteeing the synchronization and the correct update of all applications.
- Any device, anytime
The way people work is changing, as are expectations of how and where they do it. With a PLM in the cloud, users are no longer tied to their office; they can access information from anywhere, at any time and on any device. Even in transit from mobile devices.
- Lower entry costs
You do not need to invest in hardware resources to implement a PLM in the cloud, and therefore neither in their support and maintenance. Adding that current PLMs require less customization and development, this translates into lower implementation costs. The initial investment is low, so the entry barrier for the implementation of a PDM in the cloud is low.
- Boost collaboration and promote innovation
The optimization of access to information, extended collaboration to external people, the simplification of implementation and training, allow focusing efforts on business goals such as improving competitiveness and innovation.
On the other hand, the disadvantages that can be:
- Communication and collaboration
The communication and collaboration functions are limited to users of the platform, and it is necessary to have access to it to participate in the communities, collaborate and share information.
To download documents, users external to the platform will need to register (to access without a license) and they will only be able to view and download the document. The notifications must be received from email.
- Cloud platform
It is necessary to have an internet connection to be able to access the platform and its information.
Only in the case of design tools (which are installed locally) can the work be done without connection, saving the progress in a local cache until the connection is re-established.
- User licenses
It is a SaaS (Software as a Service) solution. It is not a purchased solution; it is paid per use on a quarterly or annual basis. Licensing is by named user (each user has the license for it) and not by concurrent users (maximum limit of users who access the system simultaneously).
In an educational environment, this can be an inconvenience because with the licenses per user, as many licenses as students are needed.
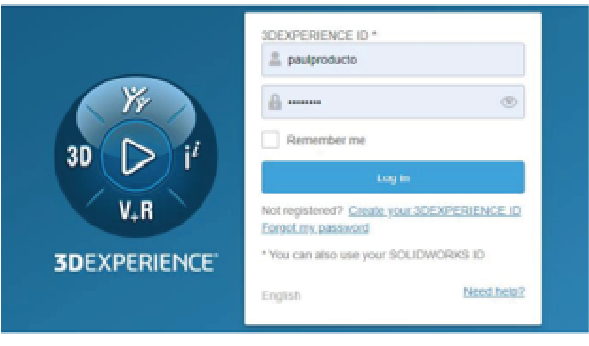
Figure 23: 3DEXPERIENCE Log In. Source: Ibermática
COMPETENCES ADDRESSED WITH 3DEXPERIENCE PLM
3DEXPERIENCE Edu is the Dassault Systèmes’ Education Department – an exciting new world available in My3DEXPERIENCE to help school children, students, teachers and professionals level up their lifelong learning and boost their employability and innovation power.
The current global situation has brought challenges to every aspect of our lives, and education is no exception. These are unprecedented times and everyone – from academic institutions to teachers, students, companies and professionals – must adjust and adapt. Teachers have become students, required to learn how to move their daily job online. School children and students must complete their schoolwork and lab activities from home, working collaboratively with their classmates, while meeting deadlines set by their teachers. Professionals must continuously upgrade their skills to be ready for the much needed business transformation.
The value of 3DEXPERIENCE Edu hinges on the diversity of its community – schoolchildren, students, teachers and professionals all aiming for the same goal: reinvent the way we learn, teach, make & share to imagine sustainable innovations.
More information in https://edu.3ds.com/en
As for the student resource bank, there is a complete set of applications, content and services aimed at students:
- Learning Portal https://eduspace.3ds.com/3DEXPERIENCE
Edu Space is a unique online learning portal giving you access, anywhere, anytime, to thousands of learning materials to help students, teachers and professionals become proficient in using Dassault Systèmes products and solutions.
- Certification https://edu.3ds.com/en/be-recognized
Certifications provide talented students and individuals with the recognition of their skills in using our solutions to further increase their employability. Two levels of certification are available:
1. Associate certification (attests the acquisition of knowledge and skills during learning activities)
2. Professional certification (attests the capacity to perform in a job role in a professional environment)
- Job Place https://edu.3ds.com/en/job-place
Discover job opportunities connected to your Dassault Systèmes skills and get inspired by success stories from power users. Currently 459 job offers in Spain and 6,602 worldwide.
3DEXPERIENCE Edu HUB https://edu.3ds.com/en/hub
The hub is a dedicated place for those who need inspiration for their project. Every year, this is where we develop advanced projects using the 3DEXPERIENCE platform. Students will find learning content and materials here.
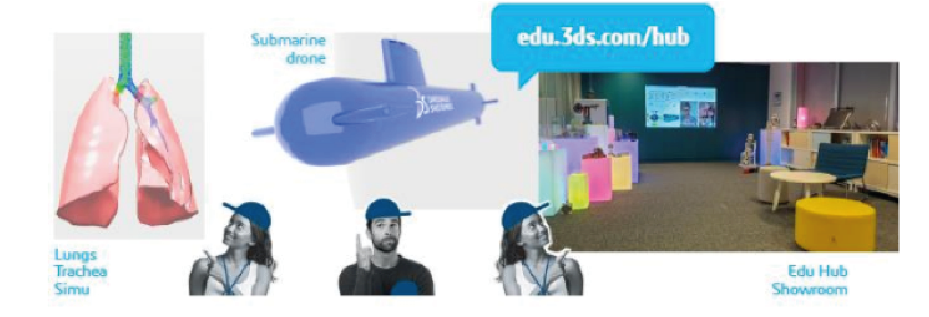
Figure 24: 3DEXPERIENCE Edu HUB. Source: Ibermática
Skills of the future https://edu.3ds.com/en/job/skills
Technologies are reshaping the world of work. Jobs are being transformed and new jobs requiring new skills are emerging. We have started a series of publications called “Skills Wanted for Sustainable Innovations” aimed at sharing the views of 3DEXPERIENCE Edu and our ecosystem on the ongoing changes in key roles and skills.
Challenges https://edu.3ds.com/en/challenges
Dassault Systèmes is proud to enable people from all over the world to compete international challenges. We sponsor and organize major competitions where students are asked to design humanoid robots, electric-powered submarines, solar racecars, next-generation drones and even space shuttles.
Communities, Social Networks https://go.3ds.com/studentcommunity
This is the place where all students using the 3DEXPERIENCE platform can discuss ideas, share their work and get help when needed from our experts.

Figure 25: 3DEXPERIENCE social media. Source: Ibermática
As a teacher resource bank, in addition to accessing the same content that is available to students, there are exclusive applications, content and services for teachers:
3DEXPERIENCE Edu Centers https://edu.3ds.com/en/edu-centers
3DEXPERIENCE Edu Centers are facilities run by Dassault Systèmes partners, where up-to-date, industry-relevant 3DEXPERIENCE knowledge and know-how is combined with their own expertise and provided for learners through initial or continuing learning programs.
Academy Member Program https://edu.3ds.com/en/be-recognized
The “Dassault Systèmes Academy Member Label” program acknowledges academic institutions engaged in using Dassault Systèmes 3DEXPERIENCE platform, CATIA, SOLIDWORKS or SIMULIA software in their study programs and which have shown a committed effort to leveraging the benefits of DS tools for student employability and curriculum quality. This recognition is disseminated throughout our global ecosystem.
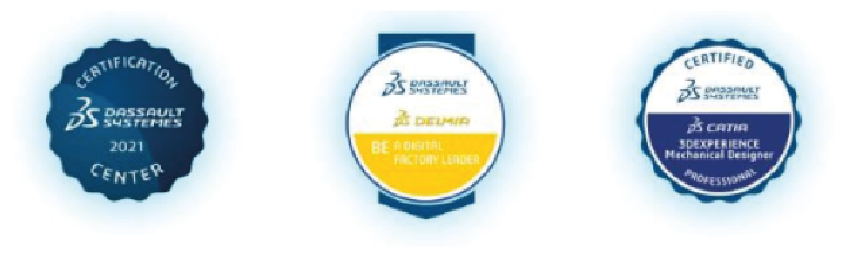
Figure 26: 3DEXPERIENCE certifications. Source: Ibermática
Certification & Ecosystem https://edu.3ds.com/en/be-recognized
To constantly enhance our understanding of educational needs and trends, Dassault Systèmes fosters strong relationships with engineering education societies, among which. For example:
- American Society for Engineering Education (ASEE)
- International Federation of Engineering Education Societies (IFEES)
- Global Engineering Deans Council (GEDC)
- European Society for Engineering Education (SEFI)
- Indo Universal Collaboration for Engineering Education (IUCEE)
- Japanese Society for Engineering Education (JSEE)
- Korean Society for Engineering Education (KSEE)
COLLABORATION OPPORTUNITIES OPENED BY 3DEXPERIENCE PLM
As mentioned above, the interaction of 3 main elements is essential to assure the coordination of every single element that takes part in the overall production: ERP-PLM-MES
The element itself is a collaborative facilitator but it is essential for the correct functioning of the CLF manufacturing process. On the one hand, it is the system that will give the necessary information about the product fabrication. On the other hand, it is responsible for managing all the changes that anyone does to the product. That is why, with the combination of ERP and MES, from the information it collects, it enables different production processes of different schools or countries to be known. In addition, through collaboration, these processes could be improved or new ones created.
Also, schools that do not have as much machinery or technology, could make use of the data obtained to be able to make practical cases of the different production processes.
The flexibility of the system makes it easier for other schools and other productive processes to become part of it.