Following the piloting process of Advanced Manufacturing Labs for H/VET through the Collaborative Learning Factory (hereafter CLF), the EXAM4.0 partners we have piloted 16 technologies embedded in Industry 4.0.
The following image shows the overall structure of the piloting process.
Labs for Advanced Manufacturing-CLF
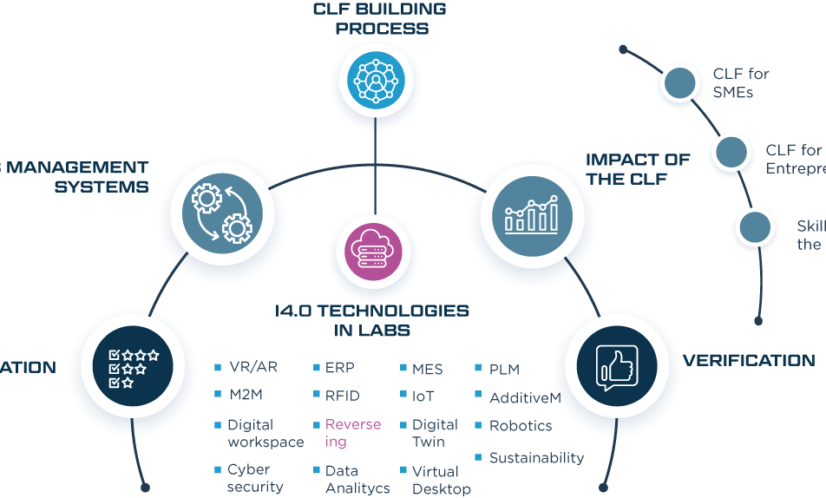
The present report is the one out of 16 I4.0 technology described within the “Industry 4.0 technologies in labs” section, specifically #4 Reverse Engineering.
DEFINITION AND APPLICATION OF REVERSE ENGINEERING IN INDUSTRY
Reverse engineering plays a vital role in the branch of mechanical design and manufacturing based industry.
This technique has been widely recognized as an important technique in the product design cycle. It is often essential to reproduce a CAD model of an existing part using any digitalization technique, when original drawings or documentation are not available. It is also useful for analysis and when modifications are required to construct an improved product design.
The product re-design with reverse engineering, will largely reduce the production period and costs in product manufacturing industries.
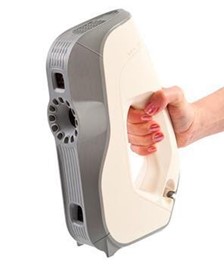
Figure 1: Inverse engineering scaner. Source: Artec EVA
Reverse engineering is the process of obtaining a geometric CAD model from measurements acquired by contact or non-contact scanning technique of an existing physical model. The typical procedure of replicating a part by reverse engineering can be the following one:
- Existing object
- Data acquisition (Contact or not contact)
- Pre-processing (Noise filtering and merging)
- Point cloud / STL data
- Feature extraction
- Segmentation and surface fitting
- CAD model
- Manufacturing process
- Finished product
A 3D scanning system is not just a 3D scanner. It is the sum of a 3D scanner, the software and, in many cases, the necessary training to know how to use it.
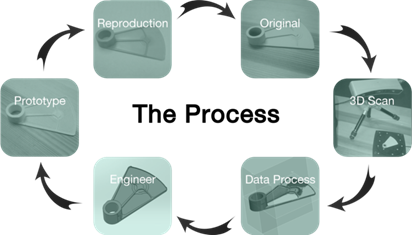
Figure 2: Inverse engineering process. Source: Siemens
Reverse engineering has a very wide range area of applications, such as:
- Mechanical engineering: product design, customization, 3D documentation
- Industrial design and manufacturing: quality control, rapid prototyping for automation and aerospace
- Health: orthopedic, prosthetics, plastic surgery, technical aids, pharmaceutical products
- Science and education: research, entertainment/animation, forensic science, online museums
- Art and design: preservation of historical heritage, architecture, fashion
- Electronics
- …
REVERSE ENGINEERING IN HVET/VET LABS
Reverse engineering has been introduced in Tknika´s IKASLAB together with Additive Manufacturing technologies, as both technologies share common advantages and combine perfectly in certain applications.
Digitalization and replication of pieces work on complex surfaces, fast prototyping: these processes and features need the combination of both technologies to go ahead with projects properly.
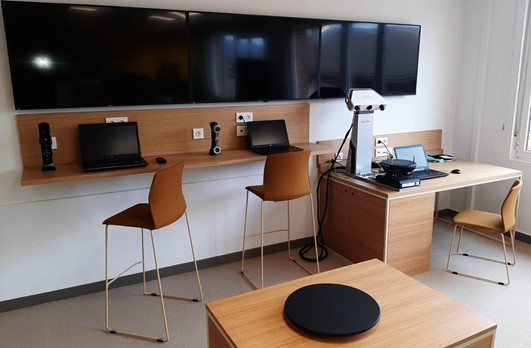
Figure 3: Tknika’s reverse engieneering lab’s overview. Source: Tknika
In the figure above Tknika’s scanning corner can be seen. It is part of the Ikaslab Project’s laboratory. Scanners from left to right: Creaform Go!Scan Spark, Creaform Handyscan 700 and Solutionix Rexcan CS+. All those scanners can be used by students of Basque VET System.
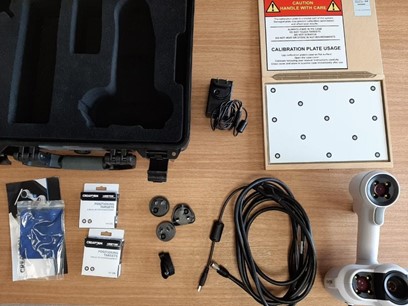
Figure 4: Creaform Academia 50 scanner equipment. Source: Tknika
Some of the scanners are fixed, it is the product to be scanned that moves, while in others, the product is still, the user moves the scanner across the surface to scan it.
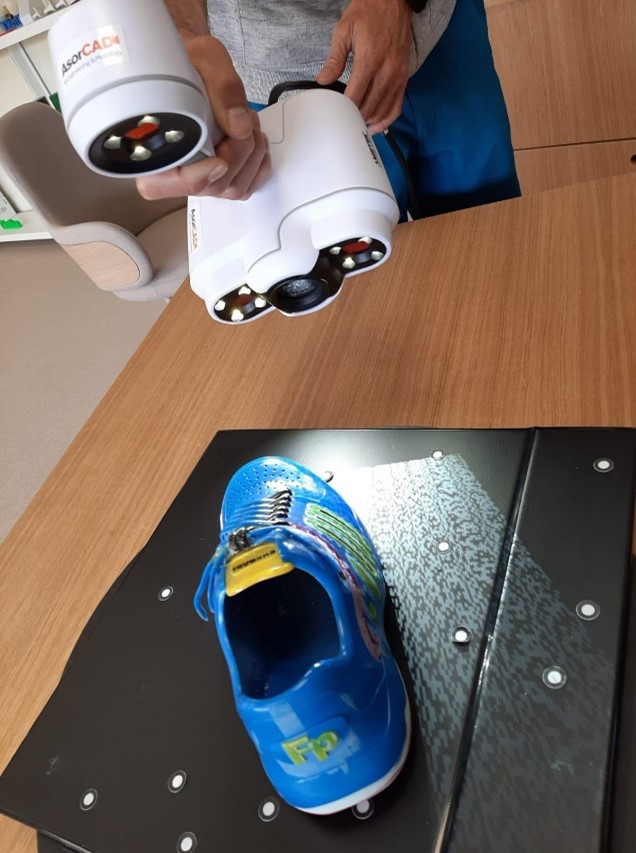
Figure 5: Scanning with Creaform Academia. Source: Tknika
Among the projects carried out with the reverse engineering scanners, one of the most important is one in which a woman’s puffed hand was scanned and custom-made prostheses were designed for her.
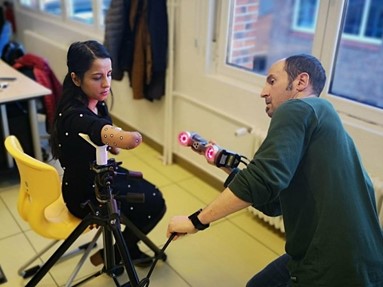
Figure 6: Scanning Maria’s arm with Creaform Handyscan 700 scanner. Source: Tknika
The processing of the scanning was made with VX Elements software and final parts with SolidWorks CAD software.
We should not forget software applications. Although they are not as visible as scanners, they are at least as important to obtain a good final digital object.
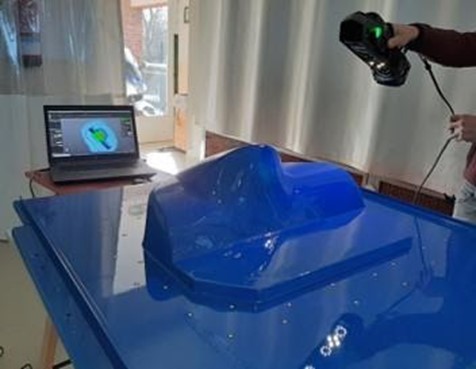
Figure 7: Scanning mould for carbon fiber part with Creaform Go!Scan Spark scanner. Source: Tknika
The software’s used in Tknika are:
- Ezscan: scanning and processing of cloud of points for Solutionix Rexcan CS+ scanner.
- VX Elements: scanning and processing of cloud of points for all Creaform scanners. It Comes together with VX Model to develop reverse engineering process and VX Inspect, which allows contrasting a reference model part.
- Polyworks: advanced industrial inspection software that combined with a handheld scanner can help in part inspection after or during a manufacturing process.
- Geomagic Design X: complete reconstruction of geometries beginning from a scanned part.
The CLF that is going to be launched has divided its production process into 4 stages (product design, process engineering, production and assembly) as can be seen in the following image. Within these stages, reverse engineering is going to be incorporated in the design and production stage.
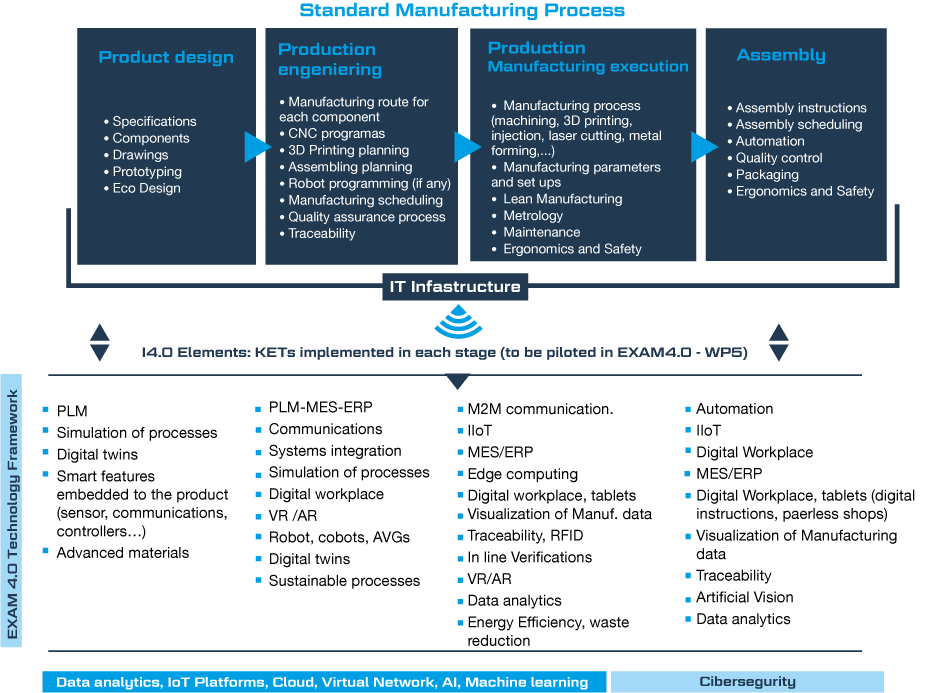
Figure 7: Exam 4.0 manufacturing process. Source: Author’s creation
The CLF we are addressing requires precise systems that convert physical pieces into mathematical models. Because of this, it is essential to have digitizing systems to be able to create digital models of the pieces. In this way, the verification of correct parts could be achieved by means of comparison to a digital pattern. The scanner could be used to digitize the parts.
The fact of digitizing the parts that are made in the manufacture of the CLF with the scanner, makes it possible to analyse design or manufacturing errors that arise. In this way, the relevant changes can be made in the designs of the parts based on the real digital model.
Finally, customizations could be made in the robots that are created in the CLF, since we could create claws, fasteners … adapted to the individual products that the user requests by scanning the products.
The major benefit of using Reverse Engineering processes is to facilitate and accelerate digitalisation processes. The knowledge and practice with the technology will allow easier detection of its applicability.
These benefits will increase even more when upcoming generative design or topology optimization processes are progressively introduced in industry.
Next generation of automatic or intelligent production systems can also introduce this technology as part of the process, integrating the scanner to a collaborative robot, for example.
These benefits can be obtained when introducing Reverse Engineering in an industrial process, which is being reproduced in each project developed in the lab:
- Increase efficiency
- Reduce errors
- Improve security
- Reduce costs
- Share information
The applicability of Reverse Engineering can be very wide and can touch different industrial areas. The competences that students can achieve are:
- Analyse different types of scanners/technologies and discover the applications of it.
- Perform the reverse engineering process: cloud of dots, mesh, solid.
- Experiment with different applications: reconstruction considering scanned part’s forms, transformation and redesign of new functionalities. Comparison of measurements.
- Experiment with different software’s, depending on the application to develop.
COLLABORATION OPPORTUNITIES OPENED BY REVERSE ENGINEERING
As another tool which is part of 4.0 industry technologies, every sharing action of the learning process and its integration in education will help to improve this process itself and make it more efficient.
This is one of the outcomes of the 3D maker. Community evolution and education systems should learn from them; how they boost the development and share knowledge:
- Selection and use of scanners and software.
- Selecting technology for each need or application.
- Share of case studies.