Following the piloting process of Advanced Manufacturing Labs for H/VET through the Collaborative Learning Factory (hereafter CLF), the EXAM4.0 partners we have piloted 16 technologies embedded in Industry 4.0.
The following image shows the overall structure of the piloting process.
Labs for Advanced Manufacturing-CLF
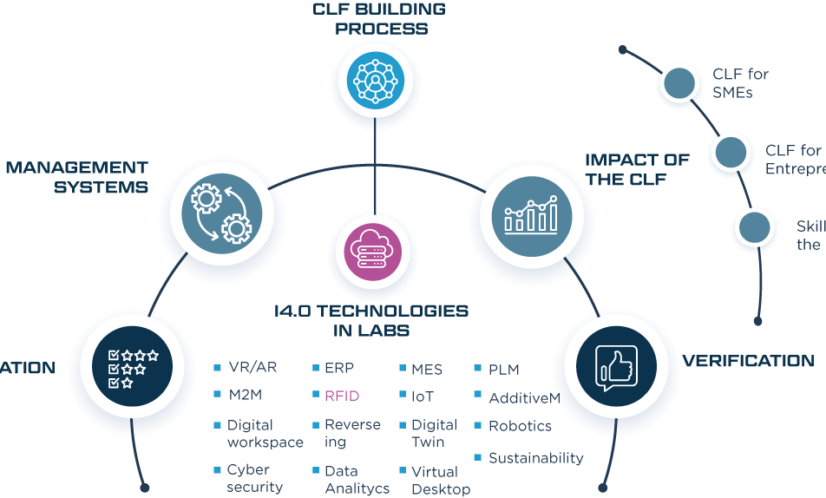
The present report is the one out of 16 I4.0 technology described within the “Industry 4.0 technologies in labs” section, specifically #8 RFID
DEFINITION AND APPLICATION OF RFID IN INDUSTRY
RFID technology is a form of wireless communication between a reader and a transmitter. It can be compared to a barcode, although radio waves are used instead of ink marks. In fact, tags with this technology are widely used in the industry, both to locate objects and to ensure that these are not removed from an establishment without the pertinent permits (VIU, 2021).
RFID systems are classified depending on the frequency range they use. There are four types of systems: low frequency (LF: 125 or 134.2 kHz); high frequency (HF: 13.56 MHz); ultra-high frequency (UHF: 868 to 956 MHz); and microwave (2.45 gigahertz) (RFID, 2021). In the case of Miguel Altuna, a card is used that combines an HF RFID with a UHF RFID. This is possible because a UHF-type RFID sticker has been attached to an HF-type RFID card. Through an application, the two types of RFID are registered in the name of a user.
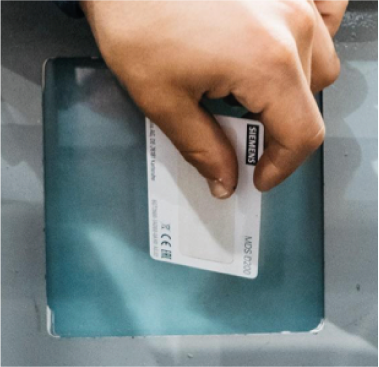
Figure 1: Miguel Altunas teacher/student RFID card. Source: author’s creation
The use of RFID technology has been expanding in recent years. Use in manufacturing is aimed at increasing the efficiency of manufacturing processes. RFID technology offers the possibility of improving efficiency in aspects such as the traceability of tools and assets, or the monitoring of devices. In another area such as the supply chain or logistics, a great commitment to RFID technology is also being done. For example, automatic quality control in the delivery of goods, or real-time checking of the status of shipments, offer new possibilities in this industry.
At Miguel Altuna, the use of RFID focuses on two main aspects, on the one hand, user control and machine booking, and on the other, tool control.
RFID IN HVET/VET LABS
At Miguel Altuna’s lab the use of RFID is focused on 2 sections. On the one hand, there is the user control, where by means of an HF RFID card the booking of the machines and the entrance to the smart warehouse are controlled. On the other hand, the tool control, where the location of the tool in the smart warehouse and which student removes each tool through the UHF RFID card is controlled. Both use cases will be explained below.
When it comes to user control, inside Miguel Altuna’s lab there are two login points. Machines can be reserved from independent posts or from the machine itself. For this, the independent points such as the machines are enabled with a HMI and a RFID reader (HF).
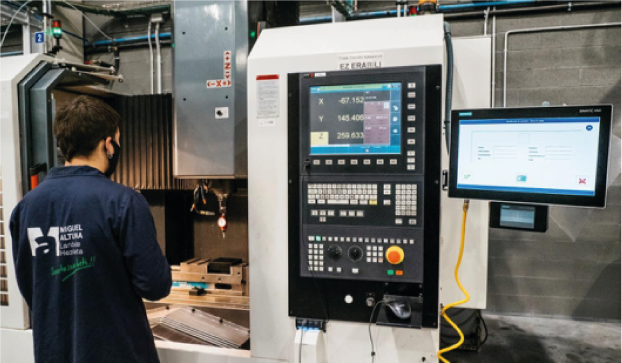
Figure 2: Student working on CNC milling machine. Source: author’s creation
Before any machine can be used, the student has to reserve it. To do this, the student will have to go to a login point and do it with their card.
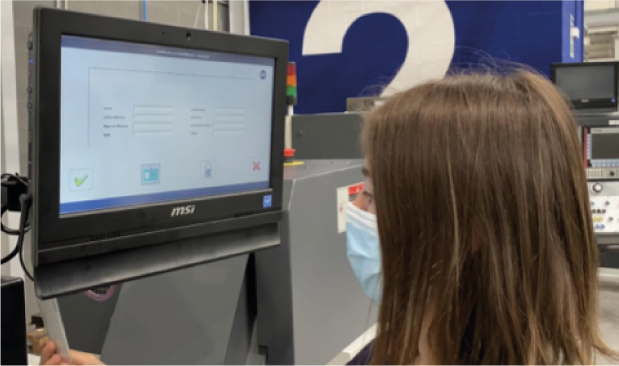
Figure 3: Student working on CNC milling machine. Source: author’s creation
The machines are divided into sections and students will have to ensure that they are wearing the corresponding security elements for the use of the machine. When booking it, the colour of a beacon installed in each machine will be changed to show that it is not available. At this time, the booking time and machine running time will begin to be counted.
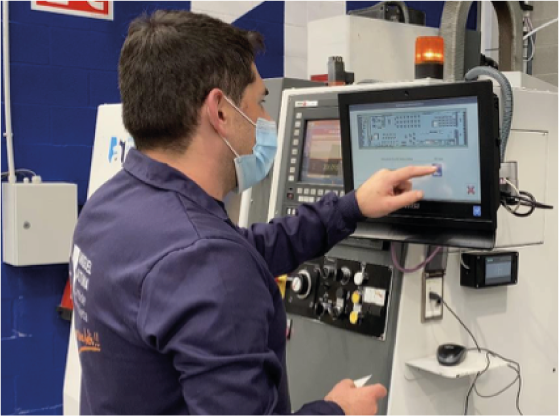
Figure 4: student confirming that he has the necessary PPE before manufacturing. Source: author’s creation
When it comes to tool control, Miguel Altuna’s lab consists of an intelligent warehouse that manages the control of the tools used by its students and teachers. This warehouse is located in the centre of the workshop to speed up people’s movements and avoid wasting a lot of time wandering around.
The entrance and exit are controlled by an RFID reading device (HF, high frequency) that identifies users and (UHF, ultra high frequency) tools.
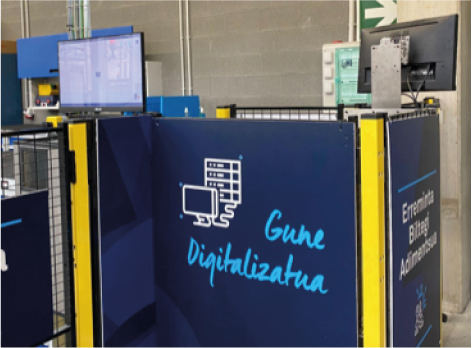
Figure 5: Smart warehouse entrance of Miguel Altuna’s lab using RFID system. Source: author’s creation
The tools inside are arranged in different cabinets with numbered drawers. The drawers are filled with identifiers and foam cut with the shape of the tool to make it easier to find the right place. All these tools are fitted with RFID tags for traceability.
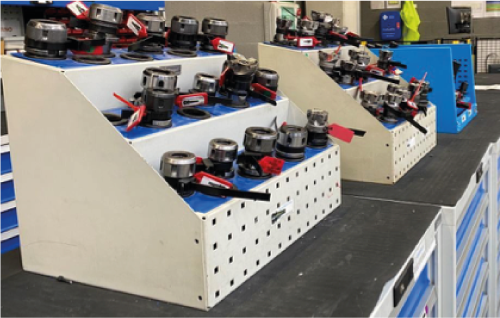
Figure 6: Tools classified by RFID system in Miguel Altuna’s lab. Source: author’s creation
The inventory of the tools in this warehouse is made on a computer inside the warehouse. This computer, in addition to storing the warehouse inventories, is used to manage the warehouse itself. It identifies the exact location of each tool, the teachers and the students associated with each teacher.
The use of this warehouse is divided into three situations: Inputs, queries and outputs.
- ENTRY. The user has to bring the personal RFID card close to the reader and press the button to start reading. At this point, the RFID reader system will read both the user’s card and the tool cards. An HMI device will display the user’s data, such as the tools that have been borrowed. If there are no errors, the system detects two users or the user enters with a borrowed tool, access is given and the door will open.
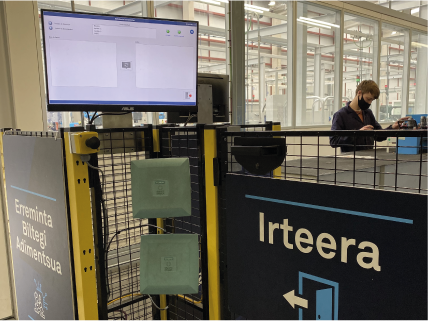
Figure 7: User and tool entry detector with RFID system in Miguel Altuna’s lab. Source: author’s creation
- QUERY. Within the smart warehouse, in addition to returning or retrieving new tools, different queries can be made.
- Quick Enquiry without logging in. Two types of quick queries can be made without logging in. On the one hand, searches can be made by product characteristics. On the other hand, by means of an RFID reading device, it will be possible to carry out direct searches by card codes.
- Consultation as a student. The list of tools used by the user can be searched.
- Consultation as a Teacher. The teacher can track the tool records; see if a tool is inside or outside the warehouse, manage tools by users, enter tools found outside and carry out card maintenance.
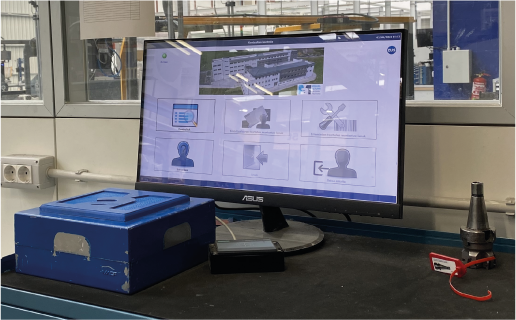
Figure 8: Consultation device using an RFID system within the intelligent warehouse of Miguel Altuna’s lab. Source: author’s creation
- EXIT. The user has to bring his personal RFID card close to the reader, like the tools to be removed, and press the button to start reading.
At this point, the RFID reader system will read both the user’s card and the cards of the tools to be removed.
An HMI device will display the user’s data, such as the tools he has removed.
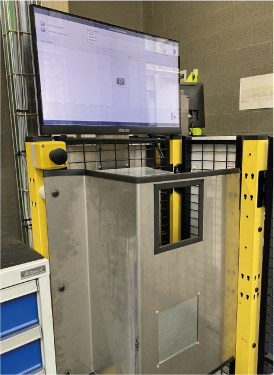
Figure 9: User and tool exit detector with RFID system in Miguel Altuna’s lab. Source: author’s creation
The CLF that is going to be launched has divided its production process into 4 stages (product design, process engineering, production and assembly) as can be seen in the following image. Within these stages, RFID is going to be incorporated in the process engineering and the production part.
Within production, the use of this element will be made when manufacturing the intermediate plates of the robot.
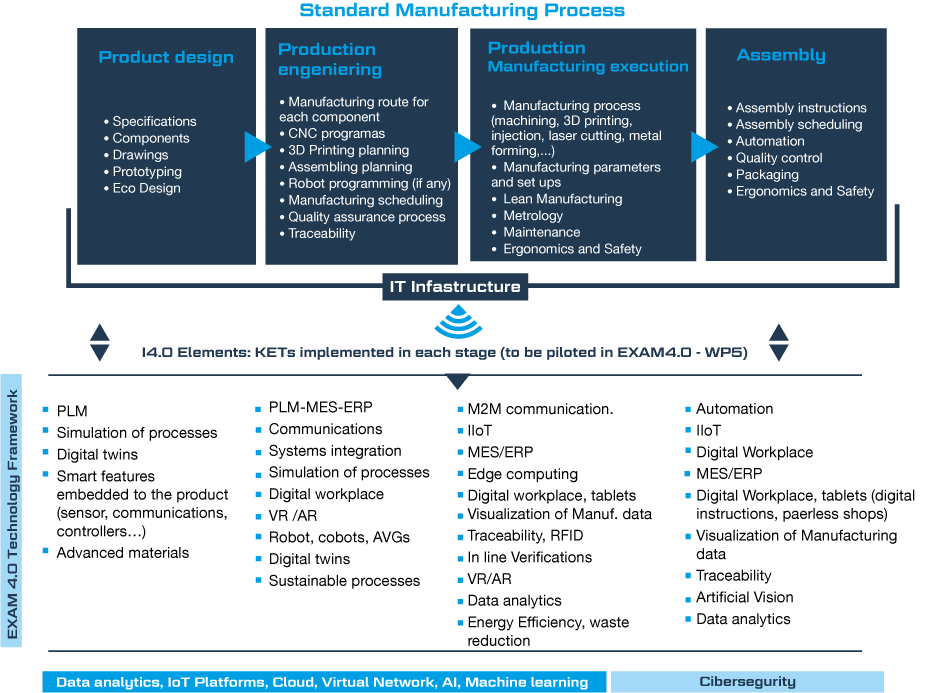
Figure 9: EXAM4.0 Collaborative Learning Factory’s (CLF) Value Chain Source: Author’s creation
First, the person in charge of making the piece will have to reserve the corresponding machine. When reserving the machine, the person in charge will upload the plans and necessary programs to make the part. From this precise moment on, it is possible to control the time that the machine has been reserved to make that piece.
Once you reserve the machine, you will have to go to the warehouse to collect the corresponding tools to make the part, as well as the material. Thus, there is a record of who has each tool. In addition, the tools needed to make the part can be related to the machine.
When manufacturing, a difference is made between the number of hours that the machine is reserved and the number of hours it is operating. In this way, it is possible to trace the hours that this tool is used to control tool wear or breakage. With the record, decisions could be made about the real needs of the tools or purchase of spare parts. In turn, if we add the total time of use of the different tools, we would have the total time that is needed to make the part.
Finally, the tool is returned to the warehouse, ensuring the return of this tool to its correct place. All the information generated will be included in the tool’s record.
The use of RFID is done in two specific processes, the control of users and tools, that is why the benefits provided by each of them will be mentioned.
When we talk about the benefits of user control, it can be said that the main benefit is to speed up the use of the workshop machines. At a glance, by means of some beacons installed in the machines, the student will be able to see which machine is occupied, damaged or free. That is why time wasted when choosing the machine is avoided.
In addition, through user recognition, each student will be assigned the machines they can use and the number of hours they can use them. In this way, the misuse of machines is avoided. As mentioned above, taking into account the issue of security, when reserving the machine, each student will have to affirm that they have all the security elements in place. With what is their responsibility to be properly equipped.
Also, it will be possible to analyse the total reservation time and the running time of the machine, thus calculating the real time that has been with each piece.
Talking about tool control & traceability, it carries a very large potential for savings, since expensive tools and components do not have to be duplicated because they are mounted in a particular assembly. In addition, having reliable information on the stock of spare parts that the workshop has is essential to minimize the amount of material in its warehouse and to be able to provide a better service to customers.
Enable knowing at any time where the tools that have been borrowed are, according to cost centre, order or machine. It also generates a complete inventory at any time and view the references most used in the workshop. Through the inventory report, it is possible to quickly obtain information on available stocks, locate references that are below stock, obtain an assessment of the stock in the warehouse, and even know the inventory of a certain date.
In addition, the control of the times of use of the tools can help in the planning of the manufacturing procedures of the different pieces.
The insertion of RFID technologies are going to help on developing competences as:
- Schedule productions, production planning, quality control and measurement procedures, maintenance planning.
- Prepare the procedures for the assembly and maintenance of equipment, defining the resources, the necessary times and the control systems.
- Supervise and / or execute the machining, assembly and maintenance processes, controlling the times and the quality of the results.
- Determine the necessary provisioning through an intelligent warehouse.
- Manage the maintenance of resources in their area.
COLLABORATION OPPORTUNITIES OPENED BY RFID
The fact of incorporating the RFID technology in laboratories opens up possible collaborations with other laboratories.
First, it is an element that generates a lot of data as mentioned above (user booking, machine time, tool traceability, etc.) and all this data can be monitored. That is why monitoring this data and using tools shared with other laboratories, can give the ability to track the parts and assembly of the parts traceability (where is it, who manufactures it, how long does it take, etc.), as well as a traceability of tools that have been used. All this helps in the calculation of costs, as well as in giving direct information to the end customer.
All this data can be used to analyse the process and improve it using digital twins. In addition, this digital twin with real data can be a perfect structure for HVETs that do not have enough (RFID, 2021) (RFID, 2021)collaboration.